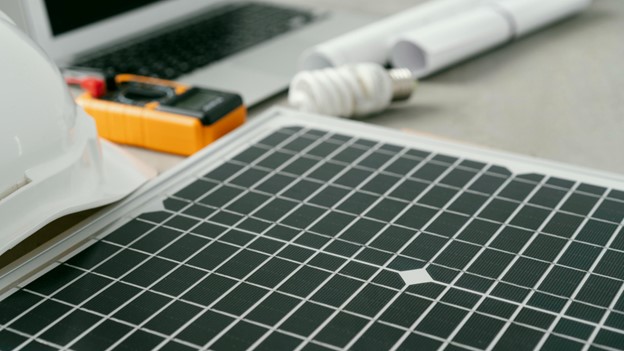
What Are the Key Components in Solar Panel Manufacturing?
The solar energy industry in India is rapidly growing, along with the country’s commitment to renewable energy and sustainability.
Solar panel manufacturing is an important part of this green movement, and understanding the key components in the production process is essential for both manufacturers and consumers. High-quality parts not only increase the efficiency and lifespan of solar panels but also contribute to the overall energy output.
Components of Solar Panel
This article explores the fundamental parts used in solar panel production and why they are important for efficient energy generation.
10 Key Components in Solar Panel Manufacturing
1. Solar Cells
The primary building block of a solar panel is the solar cell, often referred to as the heart of the system. Solar cells are usually made of silicon, which is highly effective at converting sunlight into electricity.
Below are some of the types of solar cells used in manufacturing:
- Monocrystalline Silicon Cells: Known for high efficiency and longevity, monocrystalline cells are made from a single continuous crystal structure. They are often more expensive but provide the best power output.
- Polycrystalline Silicon Cells: These cells are made from multiple silicon crystals melted together, making them more affordable but slightly less efficient than monocrystalline cells.
- Thin-Film Solar Cells: A newer, cost-effective option that is easier to produce and flexible in application. However, they have lower efficiency and are typically used in specific situations.
The efficiency of a solar panel directly depends on the type and quality of its solar cells. Choosing the right type of cell is essential for optimizing energy production.
2. Glass Layer
The glass layer serves as a protective barrier for the solar cells while allowing sunlight to pass through.
High-quality, low-iron tempered glass is commonly used for this purpose due to its transparency and strength. The glass layer must withstand various weather conditions, from intense heat to heavy rain, without compromising the efficiency of the solar panel.
India’s diverse climate makes the choice of glass critical. Factories producing panels for installation in extreme conditions, such as coastal areas, need to ensure the glass is not only durable but also designed to handle local environmental stresses.
3. Encapsulant Material
An encapsulant material, often ethylene-vinyl acetate (EVA), is used to bind and secure the solar cells within the panel. This material is crucial for protecting the cells from moisture and dust while providing a cushion that reduces the impact of vibrations and potential damage.
The encapsulant plays a significant role in extending the panel’s life. For Indian factories, choosing high-quality encapsulants ensures that panels last longer, reducing replacement costs and ensuring consistent energy output.
4. Back Sheet
The back sheet is the bottom layer of a solar panel and acts as a shield against moisture, UV rays, and other environmental factors that can degrade the panel’s performance. It also provides electrical insulation to prevent potential issues with wiring and circuitry.
The material used for the back sheet must be durable, UV-resistant, and stable under various conditions. Indian manufacturers often select materials that can handle high humidity and temperature variations, ensuring longevity and reliable performance in the diverse Indian climate.
5. Frame
A strong frame holds the solar panel together and provides stability during transportation, installation, and use. Most frames are made from aluminum, which is both lightweight and resistant to corrosion, making it ideal for outdoor installations.
The frame plays a key role in the ease of installation, especially in large-scale solar farms.
In India, where rapid installation and scalability are critical, a well-designed frame can simplify the installation process and reduce labor costs.
6. Junction Box
The junction box serves as the control center for the electrical connections within the solar panel. It houses bypass diodes, which are essential for preventing hot spots and ensuring that the panel performs efficiently even when part of it is shaded.
A quality junction box enhances the safety and functionality of a solar panel. For Indian factories, selecting junction boxes that meet international safety standards is essential to avoid malfunctions, especially in regions with unpredictable weather.
7. Wiring and Connectors
Solar panel manufacturing relies on high-quality wiring and connectors to facilitate smooth power flow. Copper or silver-plated copper is often used due to its excellent conductivity. Reliable wiring and connectors are essential to minimize energy loss and ensure safety.
India’s harsh sunlight and high temperatures can cause rapid wear in substandard wiring. Choosing high-quality materials for wiring and connectors in factories is vital to ensure durability and reduce maintenance costs.
8. Inverters
Although not part of the solar panel itself, the inverter is a critical component in a solar power system. It converts the direct current (DC) generated by the solar cells into alternating current (AC), which can be used in homes and businesses.
Different types of inverters, including string inverters, microinverters, and power optimizers, are available to suit various system sizes and needs. The choice of inverter depends on the specific requirements of the installation site and the type of panel used.
Indian solar manufacturers often work closely with inverter suppliers to ensure compatibility and optimal performance.
9. Mounting System
The mounting system is essential for securing the solar panels in place, whether on a rooftop, a ground installation, or a solar farm. Proper mounting allows panels to be oriented for maximum sunlight exposure, which is particularly important in India’s varied geographical regions.
Mounting systems are made of aluminum or steel, chosen for their durability and resistance to environmental conditions. The angle and positioning of the panels play a key role in maximizing energy production, especially in locations where sunlight availability varies seasonally.
10. Quality Control in Manufacturing
Quality control is a non-negotiable aspect of solar panel manufacturing. It includes testing each component, from cells to junction boxes, for reliability and durability.
Quality control processes can include thermal cycling tests, humidity-freeze tests, and UV exposure tests to ensure panels can withstand different environmental conditions.
In India, where solar panels must endure high temperatures, heavy rains, and occasional dust storms, stringent quality control is even more critical.
Indian manufacturers have started adopting advanced quality standards to meet both local and international demands, ensuring their products can compete globally.
Sustainability in Solar Panel Manufacturing
With the growing emphasis on sustainability, manufacturers are adopting greener practices, such as reducing waste, recycling materials, and using renewable resources in production.
Sustainability in solar panel manufacturing is not only a response to regulatory requirements but also a selling point for consumers who prioritize eco-friendly products.
Indian manufacturers are increasingly exploring ways to make their processes more sustainable, contributing to the country’s environmental goals and enhancing their appeal in the global market.
Conclusion
Solar panel manufacturing is a complex process that involves a wide range of components, each playing a critical role in ensuring efficient energy generation and durability. From solar cells and glass layers to inverters and mounting systems, every part contributes to the overall performance of the solar panel.
Investing in high-quality components and following stringent quality control standards can make Indian solar panels more reliable and competitive globally. As the industry continues to expand, manufacturers will need to innovate and adapt to meet the evolving needs of the market.
For expert consultation in designing and managing your solar panel components manufacturing projects, leading Engineering Consultancy in Ahmedabad, VMS Consultants is here to help.
Contact us to bring your vision for renewable energy manufacturing to life!