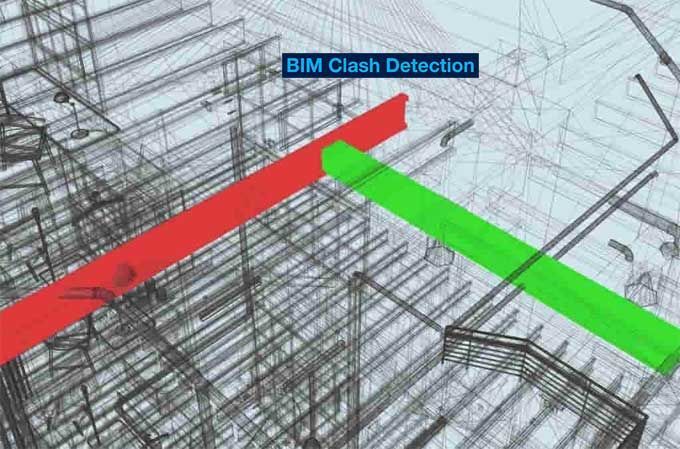
Use of BIM (Building Information Modeling) for Clash Detection at the Factory Planning Stage
In the realm of construction and industrial planning, maximizing efficiency is of utmost importance to delivering successful projects. One technology that has transformed the way factories and industrial structures are designed and built is Building Information Modeling (BIM). This innovative approach for Architecture, engineering, and Construction (AEC) enables the creation and management of three-dimensional digital representations of the physical and functional characteristics of a facility.
In particular, clash detection through Building Information modeling has emerged as a game-changer during the factory planning stage. By identifying and resolving potential clashes or conflicts early on, construction project owners can save time, reduce costs, and enhance overall project outcomes.
Understanding BIM and Clash Detection
Building Information Modeling, commonly known as BIM in its abbreviated form, is a collaborative process that integrates various aspects of a construction project into a single three-dimensional digital model. It encompasses both the physical and functional characteristics of a facility, including architecture, engineering, construction, and maintenance data. Building Information Modeling offers a comprehensive platform that allows stakeholders to visualize, analyze, and optimize their designs, resulting in more efficient construction processes.
At the heart of BIM lies clash detection, which is the process of rectifying interferences or conflicts within the building’s components. These conflicts, also known as clashes, can arise from incompatible elements such as mechanical, electrical, plumbing, architectural, and structural systems. Traditionally, these clashes were discovered during the construction phase, leading to delays in schedule, rework, and increased overall budgets.
However, with the implementation of 3D BIM modeling, clash detection can be performed during the factory planning stage of industrial, residential, or any type of structure, mitigating these issues before they become problematic for stakeholders.
Benefits of Clash Detection in Factory Planning
As learned, clash detection using 3D BIM in factory planning and construction can benefit the stakeholders by optimizing the project schedules and the overall project cost. Let us learn more about the benefits of BIM clash detection for factories and industrial buildings:-
Time and Cost Savings:
Clash detection allows for early identification and resolution of clashes in the planning stage of the factory structure. It allows for adjustments and modifications to be made in the virtual environment, eliminating the risk of issues during actual construction.
By addressing any type of conflict (hard clash, soft clash, and workflow clash) before construction begins, potential rework is minimized, saving valuable time and resources. Moreover, the reduced need for on-site alterations and modifications lowers labor costs and prevents project delays.
Enhanced Collaboration:
3D BIM modeling facilitates effective communication and collaboration between various project stakeholders, including architects, engineers, contractors, and facility owners. Clash detection permits these stakeholders to work together, rectifying and resolving conflicts in real-time. This collaborative approach to construction projects ensures that all parties are on the same page, resulting in a smooth and systematized planning process and a quality- assured outcome.
Improved Accuracy:
BIM clash detection in the factory planning stage allows for a significant level of accuracy in the design and coordination of different building systems. By identifying clashes before construction, design teams can make necessary alterations, ensuring that all components fit together seamlessly. This not only improves the overall quality of the facility but also minimizes potential risks and safety hazards.
Optimized Space Utilization:
Clash detection effectively optimizes space utilization within a factory building. By identifying clashes between equipment, machinery, and structural elements, building planners can make informed decisions regarding the layout and arrangement of these components. This optimization leads to a more efficient use of available space, improving productivity and workflow within the facility.
Future Maintenance and Upgrades:
Clash detection during the factory planning stage offers a foundation for ongoing facility maintenance and future upgrades. The three-dimensional digital model of a factory created in a BIM-based software program can be used as a reference for future repairs, replacements, or renovations, saving time and resources in the long run.
By considering BIM clash detection as part of the building planning and design process, construction project owners and construction firms can ensure that their facilities remain adaptable and future- proof.
Wrapping Up
The implementation of Building Information modeling technology and clash detection in the factory planning stage has revolutionized the construction of factories and other industrial buildings as well. By leveraging the power of digital technology, construction firms can identify and resolve clashes early on in the planning stage itself, resulting in improved efficiency, reduced costs, and enhanced collaboration among different trades on a single platform. The benefits of BIM clash detection extend beyond the planning phase, offering a solid foundation for ongoing maintenance and future upgrades.
As 3D BIM technology continues to evolve and become more widely adopted, it promises to reshape the way factories are designed, built, and operated, ensuring a brighter future for the industrial construction industry.