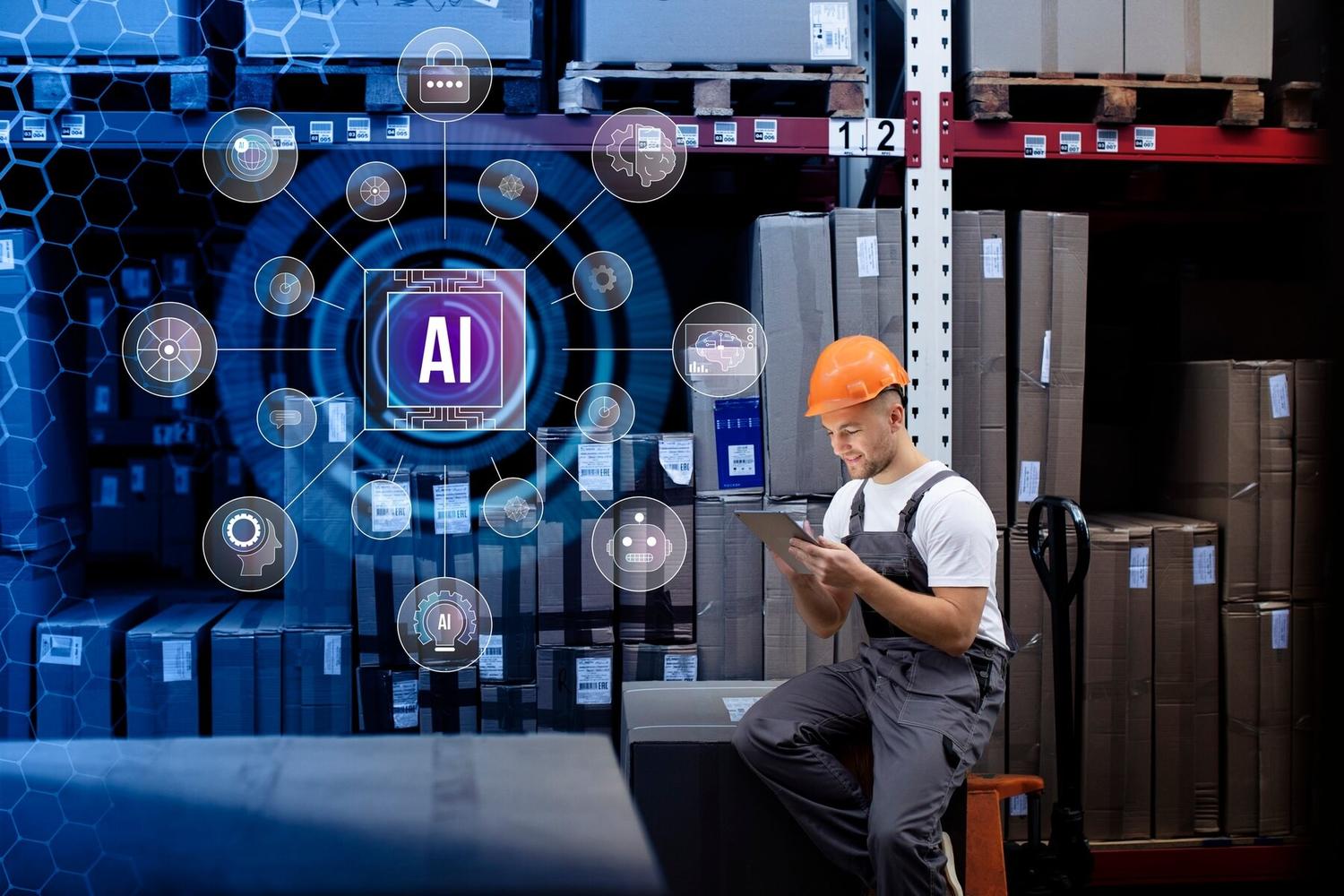
Use of AI to Prevent Machine Downtime
In today’s fast-paced industrial landscape, minimizing machine downtime is crucial for maintaining operational efficiency and meeting production targets.
However, despite advancements in maintenance practices, unexpected breakdowns continue to plague manufacturing facilities, resulting in costly downtime and lost productivity.
Fortunately, the advent of artificial intelligence (AI) has unlocked new possibilities for predictive maintenance, enabling proactive measures to prevent machine failures before they occur.
In this article, we’ll explore the power of predictiveness and how AI is revolutionizing the way we approach machine maintenance.
Understanding Predictive Maintenance:
“Predictive maintenance is a proactive approach to maintenance that leverages data analytics and machine learning algorithms to predict equipment failures before they happen.”
Unlike traditional reactive or preventive maintenance strategies, which rely on predetermined maintenance schedules or breakdowns, predictive maintenance utilizes real-time data from sensors, IoT devices, and machine learning models to identify potential issues early on.
The Role of AI in Predictive Maintenance:
Artificial intelligence plays a pivotal role in predictive maintenance by analyzing vast amounts of data to detect patterns and anomalies indicative of impending equipment failures. Machine learning algorithms can identify subtle changes in machine behavior, such as vibration patterns, temperature fluctuations, or abnormal sounds, that may precede a breakdown.
By continuously monitoring equipment performance and analyzing historical data, AI enables maintenance teams to anticipate issues and take preemptive action to prevent downtime.
Benefits of Predictive Maintenance:
The adoption of predictive maintenance offers a myriad of benefits for industrial organizations. By identifying and addressing potential issues proactively, companies can minimize unplanned downtime, reduce maintenance costs, and extend the lifespan of equipment.
Moreover, predictive maintenance enables better resource allocation by prioritizing maintenance activities based on actual equipment condition, optimizing workforce efficiency and productivity.
Real-World Applications:
Predictive maintenance powered by AI is already making waves across various industries. In manufacturing, predictive maintenance systems can analyze equipment data in real-time to detect abnormalities and trigger alerts for maintenance technicians.
In the energy sector, AI-driven predictive maintenance helps utilities anticipate and prevent equipment failures in power plants, minimizing service disruptions and ensuring reliable energy supply.
Similarly, in transportation and logistics, predictive maintenance enables fleet operators to identify maintenance needs proactively, optimizing vehicle uptime and reducing operational costs.
Challenges and Considerations:
While the potential benefits of predictive maintenance are undeniable, implementation may present challenges for some organizations. Integrating AI-powered predictive maintenance systems requires investment in technology infrastructure, data analytics capabilities, and employee training.
Additionally, ensuring data accuracy, privacy, and security is paramount when leveraging sensitive equipment data for predictive maintenance purposes.
Looking Ahead:
As AI continues to advance, the future of predictive maintenance looks promising. Emerging technologies such as edge computing, digital twins, and predictive analytics are poised to further enhance the capabilities of predictive maintenance systems, enabling even more accurate and proactive maintenance strategies.
By using the power of AI-driven predictive maintenance, industrial organizations can stay ahead of the curve, minimize downtime, and maximize operational efficiency in an increasingly competitive market.
Conclusion:
In conclusion, the power of predictiveness unleashed by AI is transforming the landscape of machine maintenance, offering unprecedented opportunities to prevent downtime and optimize equipment performance.
By embracing predictive maintenance powered by AI, industrial organizations can unlock significant cost savings, improve operational efficiency, and ensure uninterrupted production processes.
As we navigate the digital age, leveraging the potential of AI-driven predictive maintenance will be essential for staying competitive and thriving in today’s rapidly evolving industrial landscape.
Ready to harness the power of AI-driven predictive maintenance for your industrial operations? By using the expertise of VMS Consultants, a top engineering consultant in Ahmedabad, organizations can maximize the potential of AI-driven predictive maintenance systems, optimize maintenance strategies, and minimize downtime.