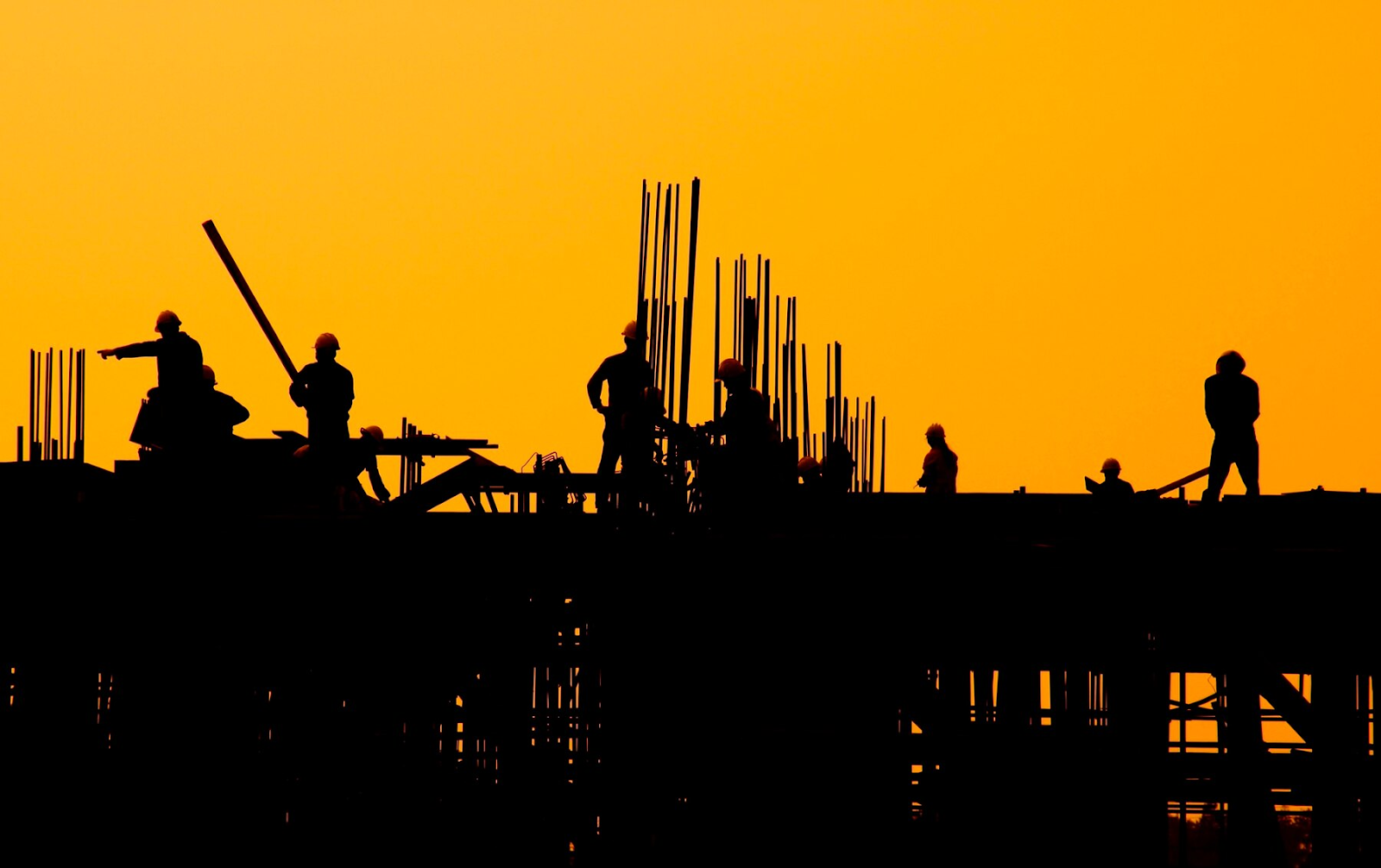
Understanding the Factory Construction Timeline: An Overview from VMS
The process of building a factory in India is exciting, but it requires meticulous planning and adherence to a well-defined schedule. Each phase of the project plays an important role in its success, from securing permits and approvals to breaking ground and building.
With the expertise and guidance of VMS Consultants, the best engineering consultant in Ahmedabad, you can navigate each stage of the factory construction timeline with ease. From initial planning to final completion, our team will ensure that every milestone is achieved efficiently and to the highest standards.
With this guide, we’ll walk you through the typical factory construction timeline, providing insights and tips to make the process go smoothly.
Understanding the Factory Construction Timeline
Factory construction timelines vary depending on project scope, size, complexity, location, and regulatory requirements. At VMS Consultants, we typically see factory construction projects take approximately 12 months.
In this timeline, there are several key phases, each with their own set of tasks, milestones, and durations. The timeline for this month may vary based on your requirements, so take it as a general guide.
Preliminary Planning (1-3 months)
During the preliminary planning phase, you’ll define project objectives, establish a budget, and select a suitable location for your factory. Conduct feasibility studies, site assessments, and environmental impact assessments to evaluate potential sites and obtain necessary approvals from local authorities.
Design and Permitting (3-6 months)
Once the site is secured, engage with architects, engineers, and designers to develop detailed plans and specifications for your factory. Obtain permits, licenses, and regulatory approvals from relevant authorities, ensuring compliance with building codes, zoning regulations, and environmental requirements.
Procurement and Material Selection (1-2 months)
Procure building materials, equipment, and supplies required for construction. Evaluate suppliers, obtain quotes, and negotiate contracts to secure competitive pricing and quality materials. Consider factors such as durability, cost-effectiveness, and availability when selecting building materials for your factory.
Site Preparation and Foundation (2-4 months)
Prepare the construction site by clearing vegetation, grading land, and setting up temporary facilities. Excavate trenches, lay foundations, and install underground utilities such as drainage, plumbing, and electrical systems. Ensure proper compaction and reinforcement to support the structural integrity of the factory.
Structural Framing and Enclosure (3-6 months)
Erect structural framing, including columns, beams, and roof trusses, to form the skeleton of the factory building. Install exterior walls, roofing systems, and insulation to enclose the structure and protect it from the elements. Coordinate with contractors and subcontractors to ensure timely completion of framing and enclosure work.
Interior Fit-Out and Finishes (2-4 months)
Complete interior fit-out and finishes to transform the empty shell into a functional factory space. Install flooring, partitions, ceilings, and lighting fixtures according to design specifications. Apply paint, coatings, and decorative elements to enhance aesthetics and create a conducive working environment for employees.
Mechanical, Electrical, and Plumbing (MEP) Installation (2-4 months)
Install mechanical, electrical, and plumbing systems to support factory operations. This includes HVAC systems, electrical wiring, lighting, fire protection, and plumbing fixtures. Coordinate MEP installation with other construction activities to ensure seamless integration and functionality.
Testing, Commissioning, and Quality Assurance (1-2 months)
Conduct thorough testing and commissioning of building systems to verify performance, functionality, and compliance with specifications. Address any defects, deficiencies, or issues identified during testing through remediation and quality assurance measures. Obtain final inspections and certifications from regulatory authorities before occupancy.
Handover and Occupancy (1-2 months)
Complete final inspections, obtain occupancy permits, and prepare for the handover of the factory to the owner. Conduct training sessions for staff on equipment operation, safety procedures, and emergency protocols. Celebrate the successful completion of the factory construction project and prepare for the commencement of operations.
Building a Factory From The Ground Up
It is important to follow a well-defined timeline for building a factory from pre-construction planning to final handover.
As you embark on your journey to build or expand your factory, consider partnering with VMS Consultants, Best factory Architect in India, providing Engineering Architecture & Project Management Services to various industrial segments.
As factory construction experts, we can help you understand the complexities, optimize project timelines, and achieve your business goals.
Get in touch with VMS Consultants today to learn how we can support your project with tailored engineering and project management solutions.