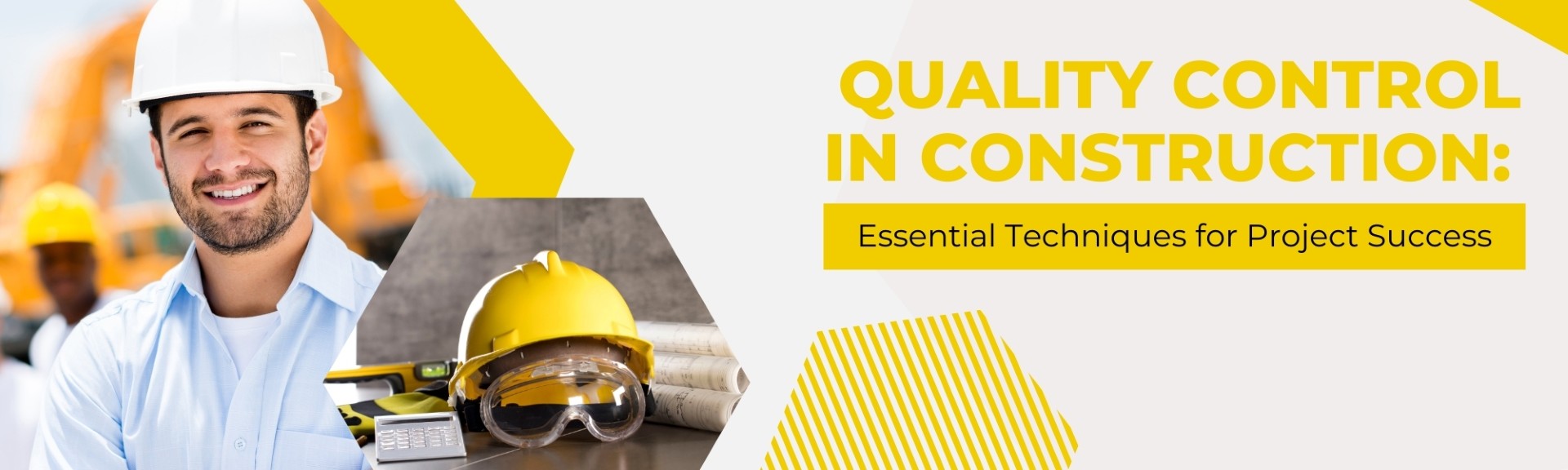
Quality Control in Construction: Essential Techniques for Project Success
General Introduction
Maintaining high-quality standards in construction is critical to ensuring project success. Effective quality control (QC) not only minimizes defects and rework but also ensures projects are completed on time and within budget. Here’s a guide to implementing successful quality control strategies that can help achieve these objectives.
- Define Clear Quality Standards
Setting clear and precise quality standards is fundamental to effective quality control. At the outset of the project, define:
– Design Specifications: Ensure that the project’s design requirements, materials, and methods are thoroughly documented and agreed upon. All stakeholders should have a clear understanding of these specifications.
– Building Codes and Regulations: Adhere to relevant local building codes and industry regulations. These standards are important for safety and legality.
- Develop a Robust Quality Control Plan
A detailed quality control plan outlines how quality will be monitored and managed throughout the construction process. Key elements include:
– QC Procedures: Define the processes for inspecting and testing materials and workmanship. Specify the frequency of inspections and identify who will conduct them.
– Documentation Protocols: Establish procedures for documenting inspections, tests, and any quality issues. Accurate records are crucial for tracking quality and addressing problems effectively.
- Employ and Train Qualified Personnel
The success of quality control heavily relies on the expertise of your team:
– Hiring Standards: Recruit skilled professionals with proven experience in quality control, including inspectors, project managers, and subcontractors.
– Training Programs: Provide ongoing training to ensure that your team stays updated on best practices, new technologies, and industry standards.
- Conduct Regular Inspections and Testing
Routine inspections and testing are vital for maintaining quality:
– Pre-Construction Inspections: Perform thorough inspections before construction begins to ensure site conditions and materials meet project requirements.
– Ongoing Inspections: Carry out regular inspections throughout the construction process to catch and address any issues promptly.
– Testing: Conduct necessary tests on materials and systems to verify they meet performance standards. This can include tests for soil, concrete, and system functionality.
- Foster Effective Communication
Effective communication among all project stakeholders is crucial for quality control:
– Regular Meetings: Hold frequent meetings with project teams, subcontractors, and clients to discuss progress and address any quality concerns.
– Reporting Systems: Implement a clear system for reporting quality issues, including a formal process for submitting and resolving non-conformance reports (NCRs).
- Address Quality Issues Promptly
Addressing quality issues as soon as they arise helps prevent larger problems:
– Issue Identification: Implement a system for quickly identifying and documenting quality issues.
– Corrective Actions: Develop and execute corrective action plans to resolve quality issues. This includes addressing the root cause and preventing recurrence.
- Manage Subcontractor Quality
Subcontractors play a significant role in overall project quality:
– Selection: Choose subcontractors with a strong track record for quality and reliability. Review their past performance and check references.
– Quality Requirements: Clearly communicate your quality expectations and requirements to subcontractors. Monitor their work to ensure compliance with these standards.
- Utilize Technology for Quality Control
Technology can significantly enhance quality control processes:
– Building Information Modeling (BIM): Use BIM to create detailed digital models of the project. This helps in visualizing potential issues and improving coordination among teams.
– Quality Control Software: Implement software solutions to streamline inspections, track issues, and manage documentation. These tools can improve efficiency and maintain comprehensive records.
- Conduct Post-Construction Reviews
Once the project is completed, conduct a review to evaluate the quality control process:
– Post-Project Evaluation: Assess the quality of the completed project against the initial standards and specifications. Identify areas for improvement and lessons learned.
– Client Feedback: Gather feedback from clients to gauge their satisfaction with the project’s quality. This feedback can be used to refine future projects.
- Embrace Continuous Improvement
Continuous improvement is key to long-term success in quality control:
– Lessons Learned: Analyze past projects to determine what worked well and what could be improved. Apply these insights to future projects.
– Ongoing Training: Invest in continuous training for your team to keep up with evolving industry standards and practices.
Wrapping Up
Quality control is integral to successful construction projects, impacting everything from safety and compliance to client satisfaction. By defining clear quality standards, developing a robust QC plan, and employing qualified personnel, you can ensure high standards are maintained throughout the project. Regular inspections, effective communication, and leveraging technology further enhance quality control efforts. With these strategies, you can achieve successful projects that meet or exceed expectations, setting the stage for future success.