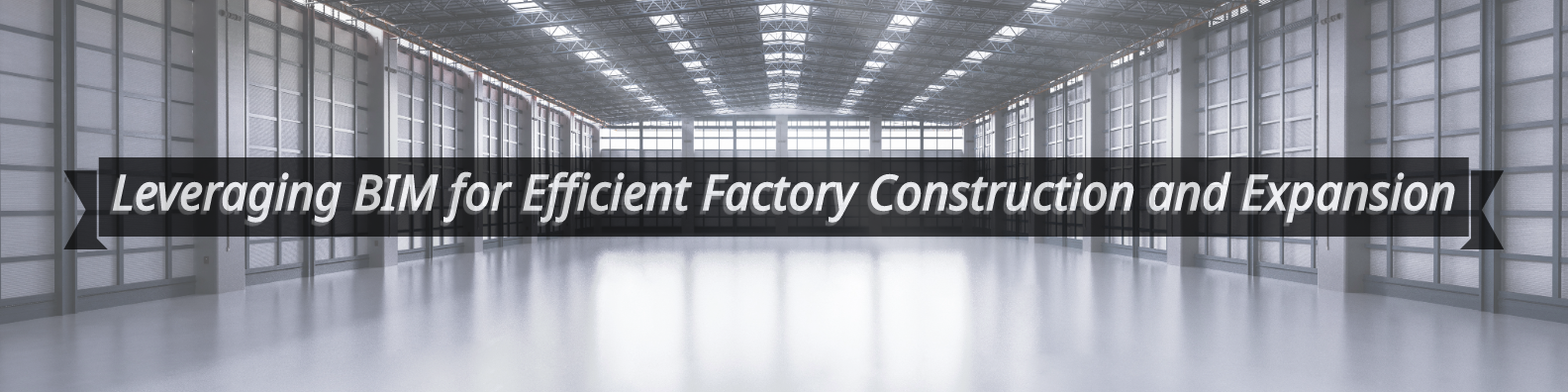
Leveraging BIM for Efficient Factory Construction and Expansion
In the realm of modern construction, BIM has emerged as a revolutionary technology, transforming the way construction projects are planned, designed, constructed, and managed. From skyscrapers to residential complexes, BIM has proven its efficacy across domains in AEC industry. However, its application in industrial projects, such as the construction of new factories and the expansion of existing factory buildings, offers a unique set of benefits and opportunities. In this article, we’ll explore how BIM can be utilized for both scenarios, ensuring optimized processes, cost savings, and enhanced project outcomes.
Understanding BIM: A Brief Overview
Before diving into its application in factory construction and expansion, it’s crucial to grasp the fundamentals of BIM. Essentially, BIM is a digital representation of physical and functional characteristics of buildings or infrastructure. 3D BIM consist of geometry, spatial relationships, geographic information, and other data. This information is stored in a shared digital model, enabling stakeholders to collaborate seamlessly throughout the project lifecycle.
Leveraging BIM for New Factory Construction
- Conceptualization and Planning:
At the outset of a new factory construction project, BIM proves invaluable in conceptualizing and planning. Architects and engineers can create detailed 3D models that simulate the entire facility, allowing stakeholders to visualize the layout, spatial arrangements, and workflow processes. Through clash detection algorithms, potential conflicts between architectural, structural, and MEP (mechanical, electrical, plumbing) systems can be identified and resolved at the design stage, mitigating costly rework during construction.
- Cost Estimation and Budgeting:
BIM facilitates accurate cost estimation and budgeting by integrating with quantity takeoff software. By associating cost data with model elements, project managers can generate precise bills of quantities (BOQ) and procurement schedules. This enables better financial planning, minimizing the risk of budget overruns and ensuring optimal resource allocation throughout the construction phase.
- Construction Management:
During the construction phase, BIM serves as a central repository of project information, facilitating effective coordination and collaboration among stakeholders. Through 4D scheduling, which integrates time-based data with the 3D model, project managers can visualize the construction sequence and identify potential scheduling conflicts. Additionally, real-time updates to the BIM model enable stakeholders to track progress, monitor project milestones, and make informed decisions to maintain project timelines.
- Facility Management and Operations:
Upon completion, the BIM model transitions into an invaluable asset for facility management and operations. Building owners can leverage the model for maintenance planning, space utilization optimization, and energy management. By integrating sensor data and IoT (Internet of Things) devices with the BIM model, predictive maintenance strategies can be implemented, prolonging the lifespan of building assets and reducing operational costs over time.
Expanding Factory Buildings with BIM
Expanding existing factory buildings presents its own set of challenges, including maintaining operational continuity, minimizing disruptions, and ensuring seamless integration with the existing infrastructure. BIM offers several advantages in this context:
- As-Built Documentation:
Before initiating the expansion project, it’s crucial to accurately document the existing structure. BIM facilitates the creation of comprehensive as-built models by capturing existing conditions through laser scanning and point cloud data. This ensures that the expansion design aligns seamlessly with the existing building geometry, minimizing conflicts and streamlining the construction process.
- Clash Detection and Coordination:
Integrating the expansion design with the existing factory building requires meticulous coordination to avoid clashes between new and old infrastructure. BIM’s clash detection capabilities enable stakeholders to identify and resolve conflicts between structural elements, MEP systems, and other components. By addressing these clashes proactively, construction delays and costly rework are minimized, ensuring smooth project execution.
- Phased Construction Planning:
To mitigate disruptions to ongoing operations, phased construction planning is essential for factory expansions. BIM facilitates the creation of detailed construction sequencing plans, allowing project managers to prioritize tasks and allocate resources efficiently. By simulating the construction sequence in a virtual environment, potential conflicts and bottlenecks can be identified and addressed before they impact the project timeline.
- Integration with Facility Management Systems:
Once the expansion is complete, the BIM model seamlessly integrates with the facility management system, providing a comprehensive digital twin of the entire factory complex. Facility managers can leverage this digital twin for space management, maintenance planning, and operational optimization. By harnessing real-time data from IoT sensors and building automation systems, proactive maintenance strategies can be implemented, ensuring optimal performance and longevity of the expanded facility.
Wrapping Up
In conclusion, Building Information Modeling (BIM) offers a plethora of benefits for both the construction of new factories and the expansion of existing factory buildings. By enabling stakeholders to collaborate effectively, visualize project outcomes, and optimize construction processes, BIM drives efficiency, cost savings, and enhanced project outcomes. From conceptualization to facility management, BIM serves as a cornerstone technology in modern industrial construction, paving the way for smarter, more sustainable factory infrastructure.