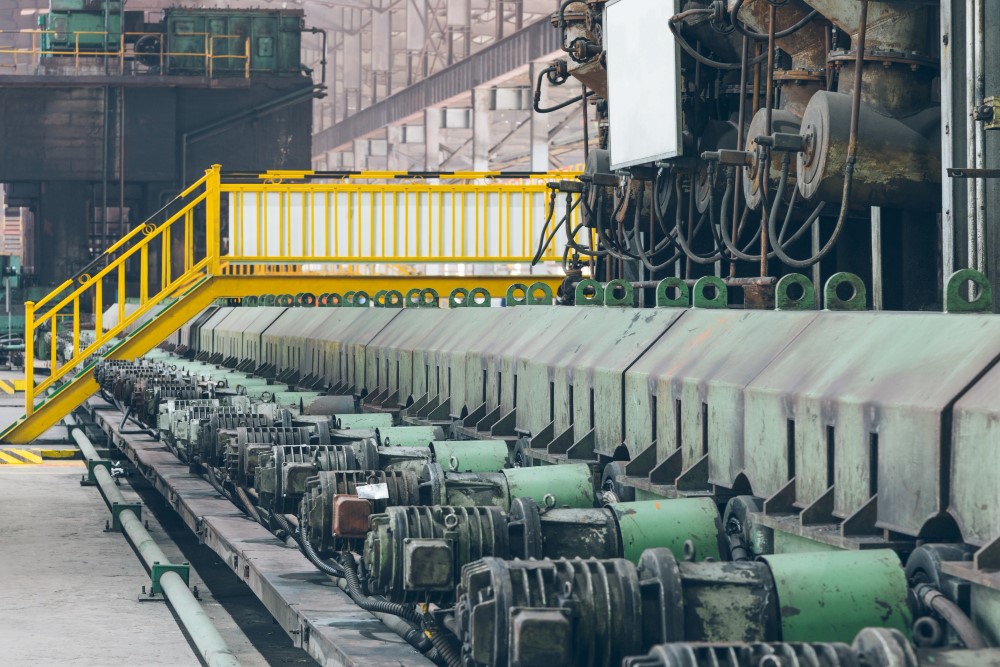
How to Streamline Material Flow in Manufacturing Plant Design?
In the ever-changing landscape of the manufacturing industry in India, optimizing operational efficiency has become increasingly important.
One key aspect that often gets overlooked but holds immense potential for improvement is the material flow within manufacturing plants.
In this article, we will explore the importance of streamlining material flow in manufacturing plant design and explore how it can enhance productivity, reduce costs, and ensure sustainable growth.
Why Streamlining Material Flow Matters
Manufacturing plants are complex ecosystems where raw materials transform into finished products through a series of intricate processes. The efficiency of this transformation largely depends on how smoothly materials move through the various stages.
Here are three reasons why streamlining material flow is essential:
1. Enhanced Productivity
Efficient material flow minimizes bottlenecks, reduces idle time, and ensures that resources are utilized optimally. This, in turn, leads to increased productivity and shorter production cycles.
2. Cost Reduction
Inefficient material flow often results in excess inventory, increased handling costs, and higher labor requirements. By streamlining material flow, manufacturers can significantly cut down on these expenses.
3. Sustainability
A well-designed material flow system can reduce energy consumption and waste generation. This not only benefits the environment but also aligns with the increasing emphasis on sustainable manufacturing practices.
Key Strategies for Streamlining Material Flow
Now that we understand the importance of optimizing material flow, let’s explore some strategies to achieve it:
1. Layout Optimization
The physical layout of a manufacturing plant plays a crucial role in material flow. It’s essential to design a layout that minimizes the distance materials need to travel between workstations. This can be achieved through careful planning and the use of tools like value stream mapping.
2. Lean Principles
Implementing lean manufacturing principles can significantly improve material flow. These principles emphasize reducing waste, which includes eliminating unnecessary inventory and minimizing transportation between processes.
Techniques like 5S (Sort, Set in order, Shine, Standardize, Sustain), Kanban, and JIT (Just-In-Time) can help eliminate waste and enhance efficiency.
3. Automation and Technology
Embracing automation and modern technology, such as conveyor systems and robotics, can streamline material handling processes. These advancements not only improve efficiency but also reduce the risk of errors.
4. Inventory Management
Effective inventory management ensures that materials are readily available when needed and prevents overstocking. Adopting just-in-time (JIT) inventory practices can be particularly beneficial.
5. Continuous Improvement
Regularly reviewing and optimizing material flow should be an ongoing process. Encourage a culture of continuous improvement within your organization to identify and address any inefficiencies.
Conclusion
A manufacturing plant design that streamlines material flow is crucial to the success of the project. In the highly competitive Indian industrial landscape, manufacturers can position themselves for success by implementing these strategies.
For expert guidance in optimizing your manufacturing plant design and material flow, consider partnering with VMS Consultants. Based in Ahmedabad, Gujarat, VMS Consultants offer Engineering Architecture and project Management Services to various industrial segments. We work on projects across India and internationally, providing comprehensive services throughout the project lifecycle, from inception to construction and commissioning.
Make a smart choice for your manufacturing business. Contact VMS Consultants today to unlock your plant’s full potential and drive sustainable growth.