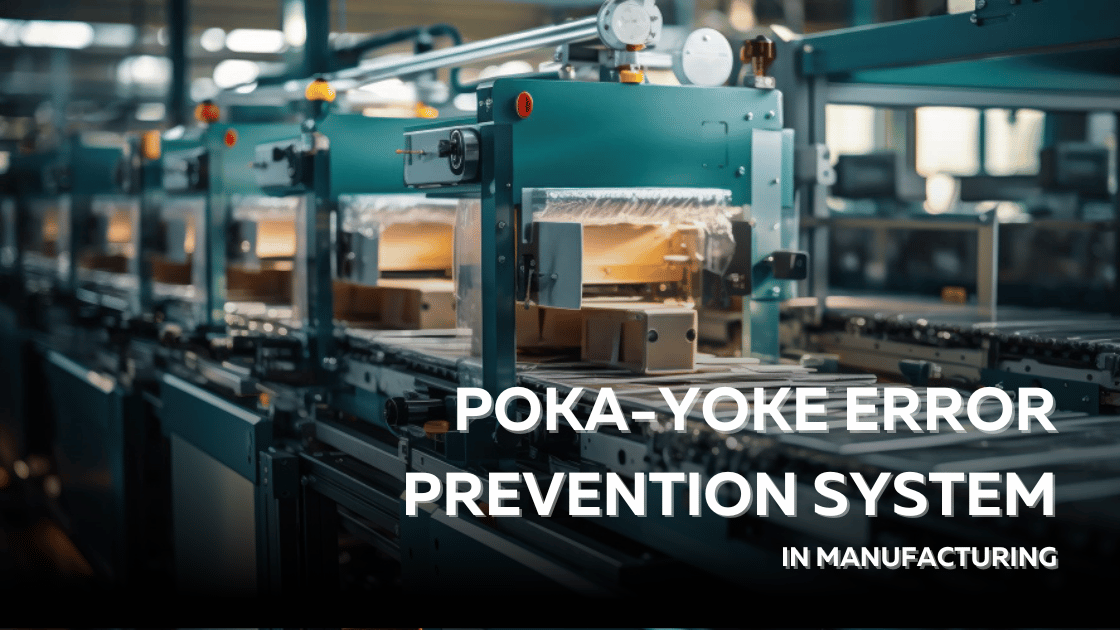
How to Implement a Poka-Yoke Error Prevention System in Manufacturing?
Poka-yoke, a Japanese term meaning “mistake-proofing,” is an effective strategy designed to help prevent errors before they occur. Integrating poka-yoke systems into manufacturing processes can improve quality control, increase efficiency, and reduce costs.
In this article, we will explore how to implement a poka-yoke error prevention system in manufacturing and the benefits it can bring.
Understanding Poka-Yoke
Poka-yoke was developed in the 1960s by Shigeo Shingo as part of the Toyota Production System. Its primary goal is to eliminate defects by designing processes in a way that prevents mistakes from happening in the first place.
Poka-yoke mechanisms can be simple devices or sophisticated systems that assist operators in ensuring quality at every step of the manufacturing process.
The essence of poka-yoke lies in creating a fail-safe environment where errors are not only reduced but can also be quickly identified and corrected. A proactive approach to quality instills a culture of quality within the organization.
Benefits of Poka-Yoke Systems
Implementing a poka-yoke system offers numerous advantages:
- Reduced Errors: By preventing mistakes before they occur, poka-yoke systems can significantly decrease the rate of defects in manufactured products.
- Increased Efficiency: With fewer errors, less time and resources are wasted on rework and corrections. This leads to smoother operations and improved productivity.
- Cost Savings: Reducing errors and defects translates to lower costs associated with waste, rework, and returns. Over time, this can have a substantial impact on a company’s bottom line.
- Improved Employee Morale: When employees can rely on a system that helps them avoid mistakes, it enhances their confidence and job satisfaction.
Steps to Implement a Poka-Yoke System
Implementing a poka-yoke system in your manufacturing process involves several key steps:
1. Identify Critical Processes
The first step in implementing a poka-yoke system is to identify the processes that are prone to errors. Look for tasks that have a high rate of defects, require a high level of skill, or are performed frequently.
By analyzing historical data and consulting with employees, you can pinpoint areas where mistakes commonly occur.
2. Analyze the Causes of Errors
Once you have identified critical processes, analyze the root causes of errors. Are they due to equipment malfunction, operator oversight, or unclear instructions?
Understanding the underlying reasons for mistakes is crucial for designing effective poka-yoke solutions.
Utilize tools like Fishbone Diagrams or the 5 Whys technique to delve deeper into the causes of errors.
3. Develop Poka-Yoke Solutions
After identifying the causes of errors, brainstorm potential poka-yoke solutions. These can range from simple tools and devices to more complex systems.
Here are some common examples:
- Physical Guides: A jig or fixture can help align parts accurately, for instance.
- Visual Aids: Use color-coded labels or diagrams to guide operators through the assembly process.
- Alarms and Sensors: As an example, a machine could stop if a part is not positioned correctly.
4. Train Employees
Training is necessary for the successful implementation of a poka-yoke system. Ensure that all employees understand the purpose and functionality of the new systems. Conduct workshops to demonstrate how to use poka-yoke tools effectively.
5. Monitor and Evaluate
After implementing the poka-yoke system, it’s important to monitor its effectiveness. Collect data on error rates and process efficiency before and after implementation.
This will help you determine if the system is achieving its intended goals.
Conclusion
In manufacturing, a poka-yoke error prevention system is a powerful way to improve quality and efficiency. Poka-yoke principles can save a company substantial costs and increase customer satisfaction.
As the Best Industrial PMC in India, VMS Consultants offers specialized engineering, architecture, and project management services tailored to various industries. Partner with us to elevate your manufacturing processes and achieve operational excellence!
Be sure to check back for more such information!