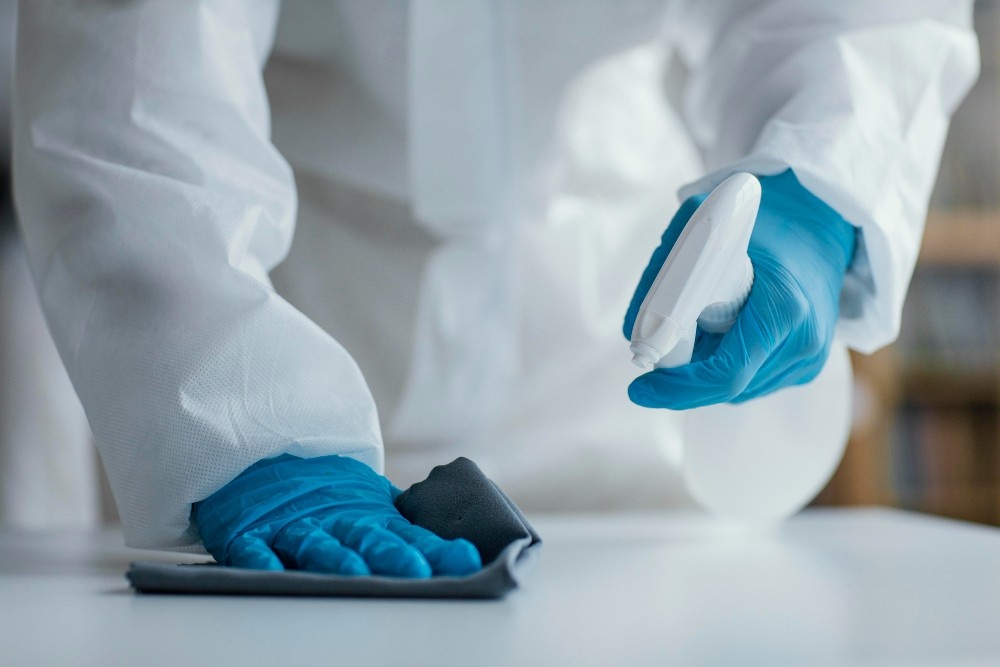
How Factory Design Affects Contamination Control in Semiconductor Cleanrooms?
Semiconductor manufacturing is one of the most precision-driven industries in the world.
Even the smallest particles of dust or airborne contaminants can compromise the performance of microchips. This is why semiconductor factories rely on cleanrooms – specially designed environments that control contamination, temperature, humidity, and air quality to ensure optimal production conditions.
In this article, we will explore the importance of cleanrooms in semiconductor manufacturing, the key design elements that help in contamination control.
Why Cleanrooms Are So Important in Semiconductor Manufacturing
Semiconductor fabrication involves multiple complex processes like photolithography, etching, doping, and deposition.
These processes require a highly controlled environment to prevent defects that could render chips non-functional.
A single particle of dust can cause a short circuit in a microchip, leading to massive production losses. Cleanrooms minimize these risks by maintaining ultra-low levels of airborne contaminants, ensuring that the manufacturing process remains precise and efficient.
5 Key Design Elements for Effective Contamination Control
1. Air Filtration Systems
One of the most critical aspects of cleanroom design is air filtration. High-Efficiency Particulate Air (HEPA) and Ultra-Low Penetration Air (ULPA) filters remove microscopic contaminants from the air.
With advanced air circulation systems, particulate levels are kept within acceptable limits with continuously supplied purified air.
In semiconductor fabs, air changes per hour can range from 100 to 600, depending on the cleanroom classification.
2. Cleanroom Classifications
Cleanrooms are classified based on the number of airborne particles per cubic meter.
Class | ISO 14644-1 Classifications |
---|---|
1 | ISO3 – 1 particle per cubic meter |
10 | ISO4 – 10 particles |
100 | ISO5 – 100 particles |
1,000 | ISO6 – 1,000 particles |
10,000 | ISO7 – 10,000 particles |
100,000 | ISO8 – 100,000 particles |
For example, a Class 100 cleanroom allows a maximum of 100 particles per cubic foot, whereas a Class 10 cleanroom allows only ten particles.
Semiconductor fabs typically operate within Class 1 to Class 100 cleanrooms to maintain extreme precision in chip manufacturing. The stricter the classification, the more stringent the contamination control measures need to be.
3. Material Selection and Surface Treatments
Every material used in a cleanroom environment must be non-shedding, non-corrosive, and easy to clean. Surfaces should be smooth to prevent particle accumulation and resistant to chemical cleaning agents.
Walls, ceilings, and floors are typically made from stainless steel or epoxy-coated materials to maintain hygiene and minimize static charge, which can attract dust.
4. Proper Airflow Management
Airflow plays a big role in contamination control. Laminar airflow systems, where air flows in a single direction at a uniform speed, help in pushing contaminants away from sensitive areas.
Unidirectional airflow combined with appropriate pressure differentials ensures that outside contaminants do not enter the cleanroom. Semiconductor fabs use positive air pressure to keep dust and microbes from infiltrating the workspace.
5. Personnel and Equipment Protocols
Humans are one of the biggest sources of contamination in cleanrooms. Employees must wear specialized cleanroom garments, including gowns, gloves, masks, and shoe covers, to prevent particles from shedding onto the production floor.
All equipment entering the cleanroom must also go through strict decontamination procedures. Even automated machinery is designed with minimal moving parts to reduce particle generation.
The Role of India in Advancing Semiconductor Cleanrooms
With India investing heavily in semiconductor manufacturing through initiatives like the India Semiconductor Mission, the adoption of world-class cleanroom technologies is becoming more common.
New semiconductor fabs in India are integrating global best practices in cleanroom design to ensure they meet international standards.
By collaborating with engineering and architecture experts like VMS Consultants, Indian manufacturers can develop state-of-the-art cleanroom facilities for high-precision production.
Challenges in Maintaining Semiconductor Cleanrooms
Despite technological advancements, maintaining contamination-free environments in cleanrooms comes with several challenges.
- High Operational Costs: Maintaining cleanrooms, especially those classified as Class 10 or lower, requires a significant investment in filtration, HVAC, and monitoring systems.
- Stringent Compliance Requirements: Semiconductor cleanrooms must comply with global standards such as ISO 14644 and US Federal Standard 209E, which necessitate regular inspections and audits.
- Training and Workforce Management: Employees need specialized training to work in cleanroom environments without introducing contamination risks. Any lapses in protocol can lead to production losses.
Future Trends in Semiconductor Cleanroom Design
With the continuous evolution of semiconductor technology, cleanroom designs are also advancing. Some key trends include:
- Smart Monitoring Systems: IoT-enabled sensors and AI-driven analytics help monitor contamination levels in real-time, allowing for proactive measures.
- Energy-Efficient Cleanrooms: To reduce operational costs, modern cleanrooms are incorporating energy-efficient HVAC systems and sustainable construction materials.
- Modular Cleanroom Designs: Prefabricated cleanrooms allow for faster installation and customization based on specific manufacturing requirements.
Conclusion
A cleanroom is one of the most important components in semiconductor manufacturing, as they ensure that contamination does not compromise the precision of manufacturing chips.
For companies planning to build semiconductor manufacturing facilities, VMS Consultants offers expert engineering, architecture, and project management services that ensure a cleanroom environment of the highest standard.