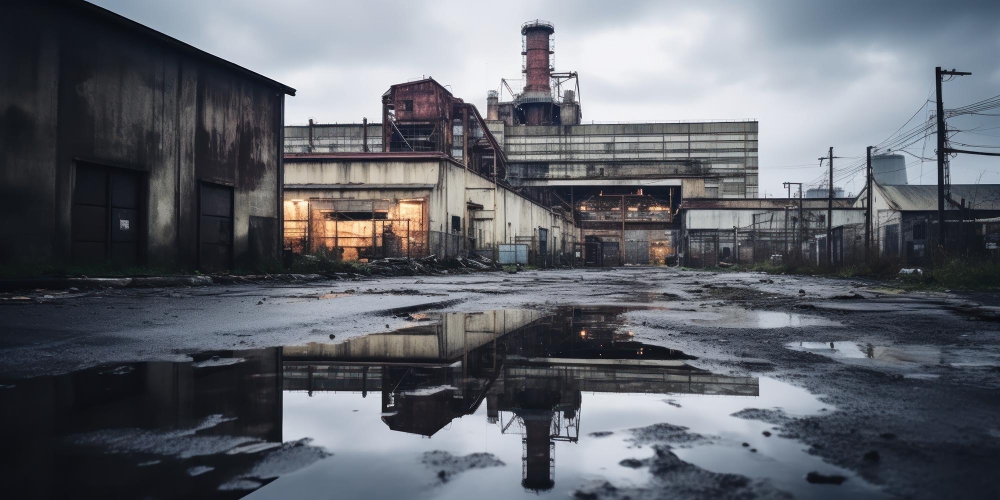
How Disaster Recovery Planning Ensures Business Continuity in Factories?
The industrial landscape is rapidly changing, and factories face numerous challenges that can disrupt operations. From natural disasters like floods, earthquakes, and cyclones to man-made crises such as fires, cyber-attacks, and power outages, the risks are ever-present.
As part of business strategy, disaster recovery planning has become increasingly important to mitigate these risks.
Having a well-structured disaster recovery plan (DRP) allows factories to quickly resume operations after an unexpected event, minimizing downtime and financial losses.
The article looks at how factories can maintain business continuity despite adversity through disaster recovery planning.
What is Disaster Recovery Planning?
Disaster recovery planning involves preparing for and responding to incidents that disrupt normal operations.
To ensure continuity of operation, customer service, and asset protection, critical functions should be restored as quickly as possible. Due to the complex nature of manufacturing processes and the reliance on technology, supply chains, and machinery, disaster recovery planning is particularly important for factories.
DRPs include several components, including risk assessments, business impact analysis, recovery strategies, and regular testing and maintenance. They all contribute to ensuring the factory can quickly recover from disruptions.
6 Components of Disaster Recovery Planning
1. Conducting a Risk Assessment
The first step in disaster recovery planning is to conduct a thorough risk assessment. This involves identifying potential threats that could disrupt factory operations and evaluating the likelihood and potential impact of these threats.
By understanding the specific risks that a factory faces, management can prioritize recovery efforts and allocate resources effectively.
2. Performing a Business Impact Analysis
Once the risks have been identified, the next step is to perform a business impact analysis (BIA). The BIA assesses the potential consequences of a disruption on the factory’s operations, finances, and reputation. It helps determine which processes and functions are critical to the factory’s survival and need to be restored first.
3. Developing Recovery Strategies
With the risks and critical functions identified, the next step is to develop recovery strategies. These strategies outline the actions that need to be taken to restore operations after a disruption.
4. Implementing Regular Testing and Maintenance
A disaster recovery plan is only as effective as its implementation. Regular testing and maintenance are crucial to ensure that the DRP remains up-to-date and functional. Factories should conduct periodic drills and simulations to test the effectiveness of their recovery strategies and identify any weaknesses or gaps.
5. Emphasizing Communication and Coordination
Effective communication is a critical component of disaster recovery planning. During a crisis, clear and timely communication with employees, customers, suppliers, and other stakeholders is essential to managing the situation and minimizing panic.
Factories should establish a communication plan that outlines how information will be shared before, during, and after a disaster.
6. Ensuring Supply Chain Resilience
For factories, disruptions in the supply chain can have a cascading effect on production and delivery schedules. Supply chain resilience is therefore a key consideration in disaster recovery planning. Factories should work closely with their suppliers to assess risks and develop contingency plans that ensure the continuous flow of materials and components.
Diversifying the supplier base, maintaining buffer stocks, and exploring alternative transportation routes are some strategies that can enhance supply chain resilience. In the event of a disruption, having multiple options for sourcing materials can reduce the impact on production.
Recover Faster with VMS
Disaster recovery planning is not just about responding to crises—it’s about building resilience and ensuring business continuity in the face of adversity. A factory’s disaster recovery plan ensures its operations, employees, and customers are protected in the event of a disaster.
VMS Consultants, leading Structural Consultant in India, offers expert disaster recovery planning services tailored to the unique needs of your factory.
Contact us today to safeguard your business continuity and ensure your factory’s resilience in the face of disaster.