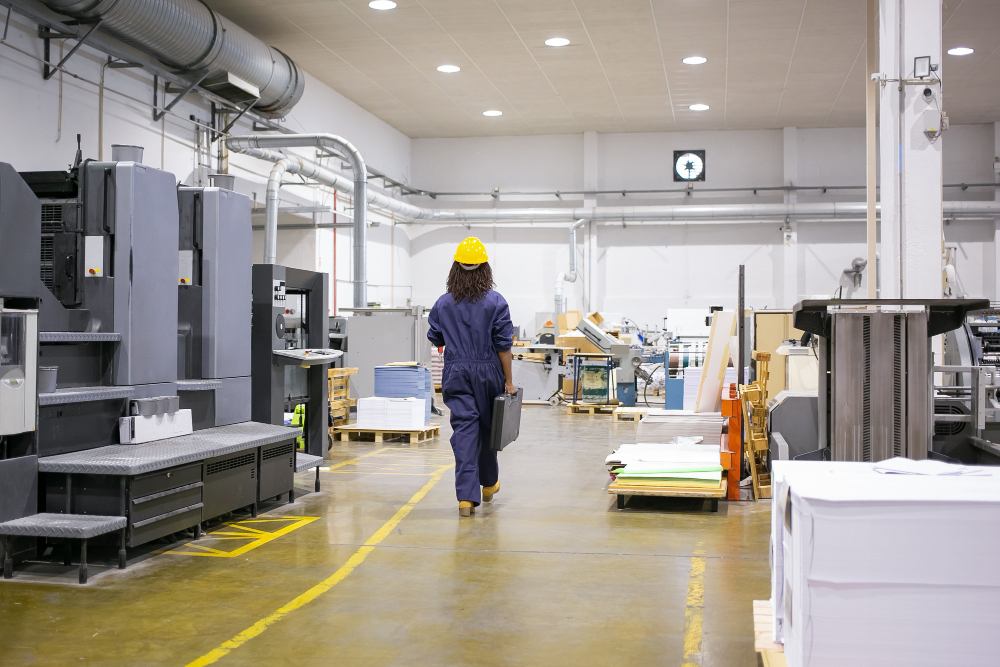
How Can You Optimize Factory Layout for Efficient Material Flow and Storage?
Optimizing material flow and implementing effective storage solutions are essential for maintaining productivity and reducing costs. The layout of a factory plays an important role in how materials move throughout the production process.
A well-designed factory layout improves both operational efficiency and employee satisfaction.
To achieve better material flow and storage solutions, we will explore key strategies for optimizing factory layouts.
Understanding Material Flow
Material flow refers to the movement of materials throughout the production process, from receiving raw materials to shipping finished products. To minimize delays and bottlenecks, this flow must be seamless and coordinated.
Key Elements of Factory Layout Optimization
1. Analyze Current Workflow
The first step in optimizing factory layout is to analyze the current workflow. Observe how materials move through the factory, identify bottlenecks, and determine which processes are causing delays. This analysis can help pinpoint areas for improvement and provide a clear understanding of the existing layout’s strengths and weaknesses.
Consider using process mapping tools to visualize the current workflow. This can reveal inefficiencies and highlight opportunities for rearranging workstations, equipment, and storage areas.
2. Consider the Type of Production
Assess the production volume, product variety, and complexity to determine the most suitable layout type. Aligning your factory layout with your production method can lead to significant efficiency gains.
3. Implement Lean Principles
Integrating lean principles into factory layout design is essential for optimizing material flow. Lean manufacturing focuses on reducing waste and improving efficiency. By organizing the factory layout around lean principles, you can streamline processes and enhance material flow.
Read more – How to Implement Lean Manufacturing Principles in Facility Design?
Consider employing techniques such as 5S (Sort, Set in Order, Shine, Standardize, Sustain) to declutter workspaces and establish a clean, organized environment.
Consider investing in technologies such as automated guided vehicles (AGVs) for transporting materials within the factory.
This helps improve safety and makes it easier for employees to locate materials.
4. Optimize Storage Solutions
The efficient storage of materials is crucial for ensuring smooth material flow. An optimized factory layout should incorporate smart storage solutions that minimize space while maximizing accessibility. Vertical storage systems, for example, can help utilize vertical space effectively.
Implementing just-in-time (JIT) inventory management can also help reduce excess inventory and streamline storage needs. This approach ensures that materials are available when needed, reducing the need for extensive storage areas.
5. Create Clear Pathways
Clear pathways are essential for facilitating efficient material movement. In an optimized factory layout, pathways should be designed to minimize congestion and promote smooth transitions between different areas.
Ensure that there are dedicated pathways for workers, materials, and equipment. This separation helps reduce the risk of accidents and ensures that materials can move freely without unnecessary delays.
Conclusion
Optimizing factory layout for efficient material flow and storage is essential for any industrial operation. The benefits extend beyond just productivity; a well-optimized layout can lead to improved employee satisfaction and a safer working environment.
With years of experience in engineering, architecture, and project management, VMS Consultants, Top industrial Architect in India, provides solutions customized to the unique needs of various industries.
Partner with us to optimize your factory layout and achieve greater operational efficiency!