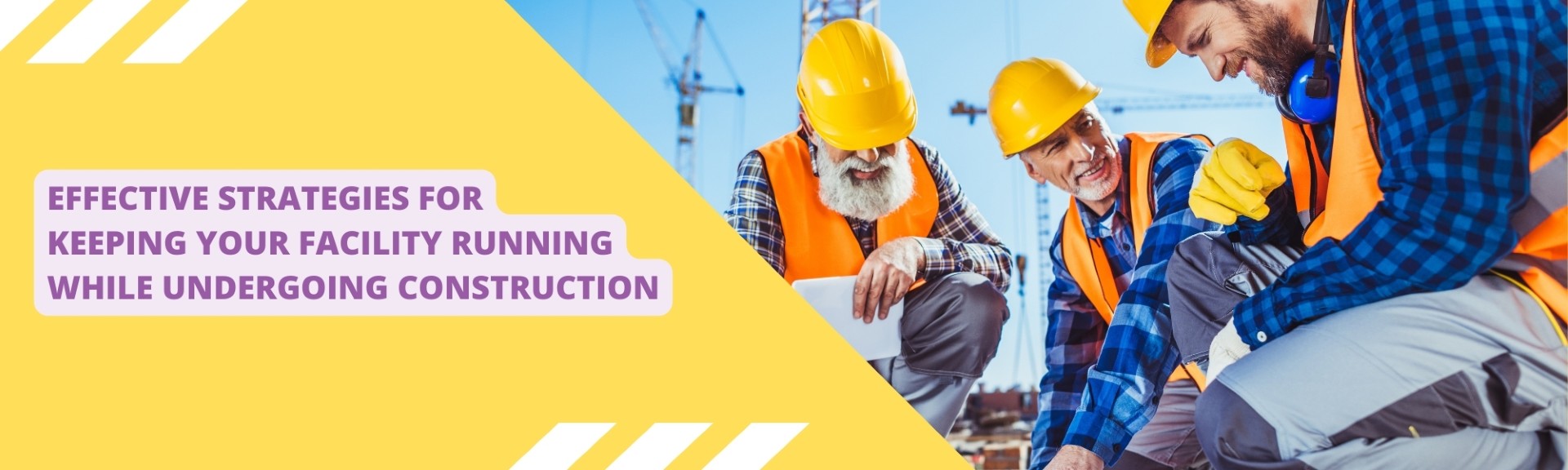
Effective Strategies for Keeping Your Facility Running While Undergoing Construction
General Introduction
When it comes to maintaining the functionality of an industrial or manufacturing facility while undergoing construction or renovation, the stakes are high. Downtime can lead to significant losses in productivity and revenue, while disruptions can affect customer satisfaction and long-term business relationships. Balancing construction needs with operational continuity requires careful planning and strategic execution. Here’s how you can keep your facility running smoothly while construction work is underway.
-
Develop a Detailed Construction Plan
A thorough plan is essential for minimizing disruptions. Work with construction managers to outline the scope, timeline, and impacts of the project. Key elements should include:
– Construction Phases: Break the work into phases to limit the impact on critical areas.
– Work Hours: Schedule construction during off-peak hours to avoid interfering with regular operations.
-
Communicate Effectively
Keep all stakeholders informed to manage expectations and reduce frustrations:
– Internal Communication: Regularly update employees on the construction schedule and any changes in workflows.
– External Communication: Notify suppliers and customers of potential delays or changes to delivery schedules.
-
Implement Temporary Solutions
To keep operations running smoothly:
– Temporary Facilities: Set up temporary workspaces or production areas if construction affects critical zones.
– Alternative Equipment: Use backup equipment to maintain production if primary machinery is affected.
-
Prioritize Safety and Compliance
Ensure safety protocols are in place to protect both construction workers and facility staff:
– Safety Protocols: Implement clear safety measures and provide training for all personnel.
– Compliance Checks: Regularly review adherence to safety regulations to avoid accidents and fines.
-
Coordinate with Construction Teams
Maintain close coordination to align construction activities with operational needs:
– On-Site Coordination: Assign a liaison to manage communication between the facility and construction teams.
– Problem Resolution: Establish a system for promptly addressing any issues that arise.
-
Monitor and Adjust Operations
Track the impact of construction on operations and adjust as needed:
– Performance Metrics: Use key performance indicators (KPIs) to monitor productivity and efficiency.
– Flexible Scheduling: Adjust work schedules and production plans based on construction progress.
-
Plan for Contingencies
Prepare for unexpected issues to minimize disruptions:
– Emergency Procedures: Develop procedures for handling construction-related incidents.
– Backup Plans: Create alternative plans for critical processes that might be affected.
-
Optimize Resource Allocation
Manage resources to balance construction needs with operational requirements:
– Resource Scheduling: Coordinate construction activities to avoid peak operational times.
– Budget Management: Monitor both construction and operational budgets to ensure adequate funding.
-
Evaluate and Learn
After construction, assess the process to improve future projects:
– Post-Project Review: Analyze what worked well and areas for improvement.
– Feedback Collection: Gather feedback from employees and stakeholders about their experiences.
Wrapping Up
Maintaining operational continuity during construction in an industrial or manufacturing facility is a challenging but achievable goal. By developing a comprehensive construction plan, communicating effectively, implementing temporary solutions, prioritizing safety, coordinating with construction teams, monitoring operations, planning for contingencies, optimizing resource allocation, and evaluating the process, you can minimize disruptions and keep your facility running smoothly. With careful planning and strategic execution, you can successfully navigate the complexities of construction while maintaining productivity and operational efficiency.