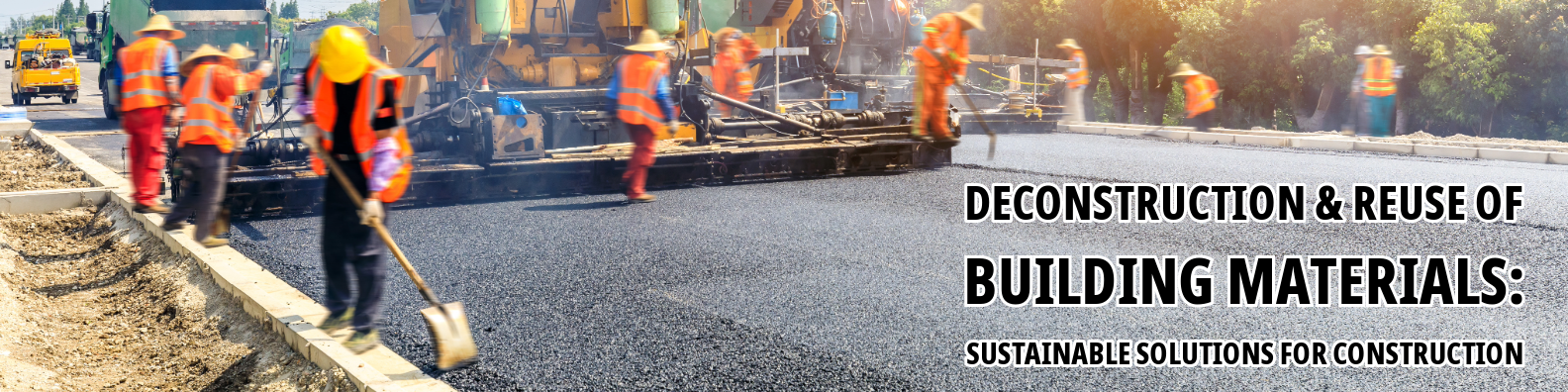
Deconstruction & Reuse of Building Materials: Sustainable Solutions for Construction
General Introduction
In the wake of environmental concerns and the urgent need for sustainable practices, the construction industry is undergoing a paradigm shift towards more eco-friendly methods. One such approach gaining momentum is the deconstruction and reuse of building materials. This innovative technique not only reduces waste but also contributes significantly to resource conservation and energy efficiency in construction projects.
Understanding Deconstruction:
Deconstruction is a systematic process of carefully dismantling structures with the aim of salvaging materials for reuse or recycling. Unlike traditional demolition, which often leads to significant waste and environmental damage, deconstruction prioritizes the preservation of valuable resources. This method involves meticulous planning, skilled labor, and the use of specialized equipment to carefully disassemble buildings while maximizing the recovery of materials.
The Benefits of Deconstruction:
- Resource Conservation: Deconstruction allows for the recovery of valuable materials such as wood, bricks, metals, and glass, which can be reused in new construction projects. By salvaging these materials, the demand for virgin resources is reduced, leading to less depletion of natural reserves.
- Waste Reduction: Traditional demolition generates vast amounts of waste, much of which ends up in landfills, contributing to pollution and environmental degradation. Deconstruction minimizes waste by salvaging materials for reuse or recycling, thereby reducing the burden on landfill sites.
- Energy Efficiency: The reuse of building materials in new construction projects requires less energy compared to manufacturing new materials from scratch. By incorporating salvaged materials, construction processes become more energy-efficient, resulting in lower carbon emissions and environmental impact.
- Cost Savings: While deconstruction may initially require more labor and time compared to conventional demolition methods, the savings achieved through material reuse and reduced waste disposal costs can outweigh the initial investment. Additionally, tax incentives and grants for sustainable construction practices further incentivize deconstruction projects.
The Deconstruction Process:
- Assessment and Planning: Before commencing deconstruction, a thorough assessment of the building is conducted to identify salvageable materials and potential hazards. A detailed deconstruction plan is then developed, outlining the sequence of activities, safety measures, and material recovery targets.
- Selective Demolition: Deconstruction begins with the careful removal of fixtures, fittings, and non-structural elements such as doors, windows, and interior finishes. This selective approach ensures the preservation of reusable materials while minimizing damage to structural components.
- Dismantling and Salvage: Skilled workers dismantle the building systematically, separating materials into categories such as wood, masonry, metals, and concrete. Salvageable materials are carefully removed, sorted, and prepared for reuse or recycling.
- Transportation and Storage: Salvaged materials are transported to storage facilities or directly to construction sites for reuse. Proper labelling and documentation are essential to ensure the efficient handling and tracking of materials throughout the process.
- Reuse and Recycling: Salvaged materials are either reused in their original form or processed for recycling. Wood can be refurbished for use in furniture or flooring, bricks can be cleaned and reused in new construction, and metals can be melted down and repurposed.
Challenges and Considerations:
While deconstruction offers numerous benefits, several challenges must be addressed to facilitate its widespread adoption:
- Cost and Time: Deconstruction projects may incur higher upfront costs and longer project durations compared to traditional demolition methods. However, long-term savings, environmental benefits, and regulatory incentives can offset these initial challenges.
- Skill and Expertise: Deconstruction requires skilled labor with expertise in handling various materials and equipment. Training programs and certifications can help develop a qualified workforce capable of executing deconstruction projects safely and efficiently.
- Regulatory Compliance: Compliance with regulations and permits governing deconstruction practices is essential to ensure safety and environmental protection. Working closely with regulatory authorities and obtaining necessary approvals is crucial for successful deconstruction projects.
- Market Demand: The demand for reclaimed building materials may vary depending on factors such as market trends, consumer preferences, and the availability of alternative materials. Creating awareness and promoting the benefits of deconstruction can stimulate demand and support market growth.
Wrapping Up
Deconstruction and reuse of building materials represent a sustainable solution for addressing the environmental challenges associated with construction activities. By adopting this approach, the construction industry can reduce waste, conserve resources, and mitigate the environmental impact of building projects. While overcoming challenges such as cost, skill, and regulatory compliance may require concerted efforts, the long-term benefits of deconstruction far outweigh the initial investments. Embracing deconstruction as a standard practice can pave the way for a more sustainable future in construction.