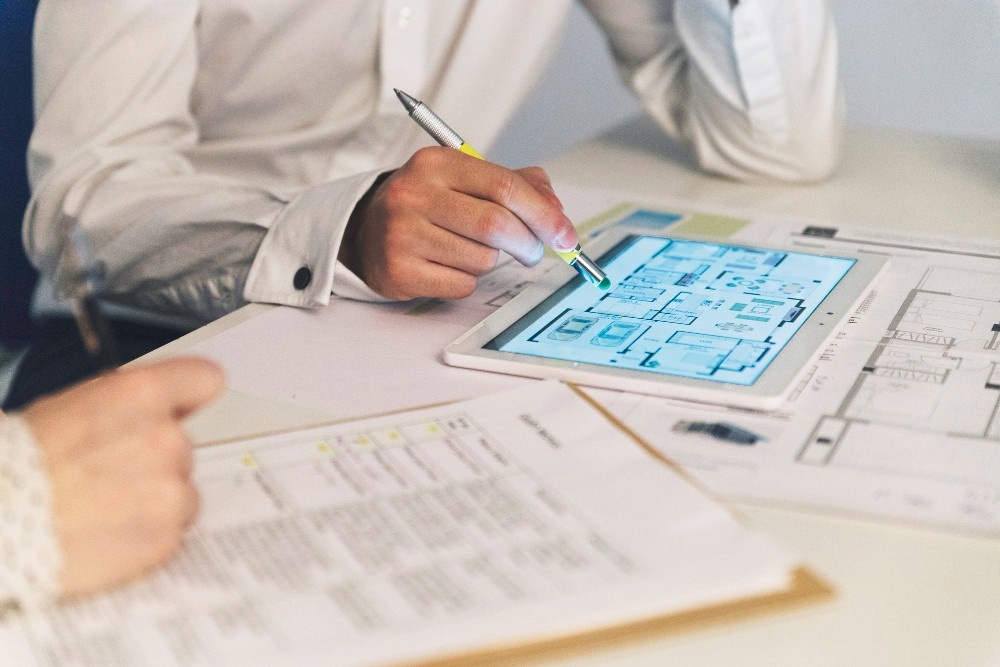
Master Planning for Semiconductor Factories: A Step-by-Step Guide
As semiconductor chip demand has increased, the world has begun to develop advanced manufacturing facilities.
A well-planned factory is important for countries aiming to become major players in the semiconductor industry. This ensures that these factories are efficient, scalable, and sustainable.
VMS Consultants is the top industrial project management consultant in India, specializing in the strategic planning and development of semiconductor manufacturing facilities and other industrial projects.
In this article, we will discuss the elements of master planning for semiconductor factories, highlighting key considerations, best practices, and India’s evolving role in this sector.
Importance of Master Planning in Semiconductor Manufacturing
Master planning involves developing a comprehensive blueprint for semiconductor factories. It covers various aspects such as layout design, infrastructure, utility management, and future expansion potential.
Given the complexity of semiconductor manufacturing, a well-thought-out master plan ensures operational efficiency, cost optimization, and compliance with environmental and safety standards.
4 Key Considerations in Master Planning
a. Site Selection
Selecting the appropriate location is the foundation of successful semiconductor factory development. Factors such as proximity to key suppliers, availability of skilled labor, access to utilities (electricity, water, and gas), and transportation infrastructure all play an important role.
In India, states like Karnataka, Tamil Nadu, and Gujarat are emerging as attractive destinations for semiconductor facilities due to their well-developed industrial ecosystems and supportive government policies.
b. Layout Design
The factory layout must be optimized for workflow efficiency. Semiconductor manufacturing involves multiple stages, including wafer fabrication, assembly, and testing. A well-organized layout minimizes material movement, reduces contamination risks, and enhances productivity.
Cleanrooms, where wafers are processed, require precise planning to ensure that air quality, temperature, and humidity are controlled at all times.
c. Utility Infrastructure
Semiconductor factories consume enormous amounts of water, electricity, and specialized gases. Ensuring uninterrupted supply and efficient management of these utilities is a core component of master planning.
For example, advanced water recycling systems can be integrated to reduce freshwater consumption, addressing environmental concerns and operational costs.
d. Environmental Compliance
Given the environmental impact of semiconductor manufacturing, adhering to stringent regulations is necessary. Master planning should include waste management systems, air quality control measures, and energy-efficient designs.
India’s focus on sustainable industrial development makes it necessary for new semiconductor factories to incorporate green building practices and renewable energy solutions.
Best Practices in Master Planning
a. Collaboration with Experts
Master planning for semiconductor factories requires expertise in various disciplines, including engineering, architecture, and project management. Engaging experienced consultants ensures every aspect is addressed.
VMS Consultants, for example, have extensive experience in delivering end-to-end solutions for industrial projects, including those in high-tech sectors.
b. Modular Design for Scalability
Semiconductor technology evolves rapidly, necessitating frequent upgrades and expansions. A modular design approach allows factories to scale operations without significant disruptions.
Planning for future phases during the initial design stage ensures that infrastructure can accommodate technological advancements and increased production capacity.
c. Risk Management
Given the capital-intensive nature of semiconductor manufacturing, risk management is a key element of master planning. This involves assessing potential risks, such as supply chain disruptions, utility failures, and regulatory changes, and developing mitigation strategies.
India’s Potential in Semiconductor Manufacturing
India’s ambition to become a global semiconductor hub has led to significant investments and policy support. The government’s Production Linked Incentive (PLI) scheme and the establishment of the India Semiconductor Mission (ISM) have created a favorable environment for setting up semiconductor factories.
With a large talent pool, competitive costs, and growing demand for electronics, India is well-positioned to attract global semiconductor manufacturers.
Companies like Vedanta and Tata Group have already announced plans to invest in chip manufacturing facilities.
Future Trends in Semiconductor Factory Design
As technology advances, semiconductor factories will continue to evolve.
Among the emerging trends are:
- Smart Factories: Integrating IoT and AI-driven systems to enhance operational efficiency and predictive maintenance.
- Sustainability Initiatives: Increasing focus on energy efficiency, water conservation, and waste reduction.
- Advanced Materials: Designing facilities capable of handling next-generation semiconductor materials, such as silicon carbide and gallium nitride.
Conclusion
Master planning is a critical step in the successful development of semiconductor factories.
As India accelerates its semiconductor journey, VMS Consultants is ideally positioned to support industrial projects with their expertise in engineering, architecture, and project management.
Partner with VMS Consultants for expert guidance and comprehensive project management solutions.