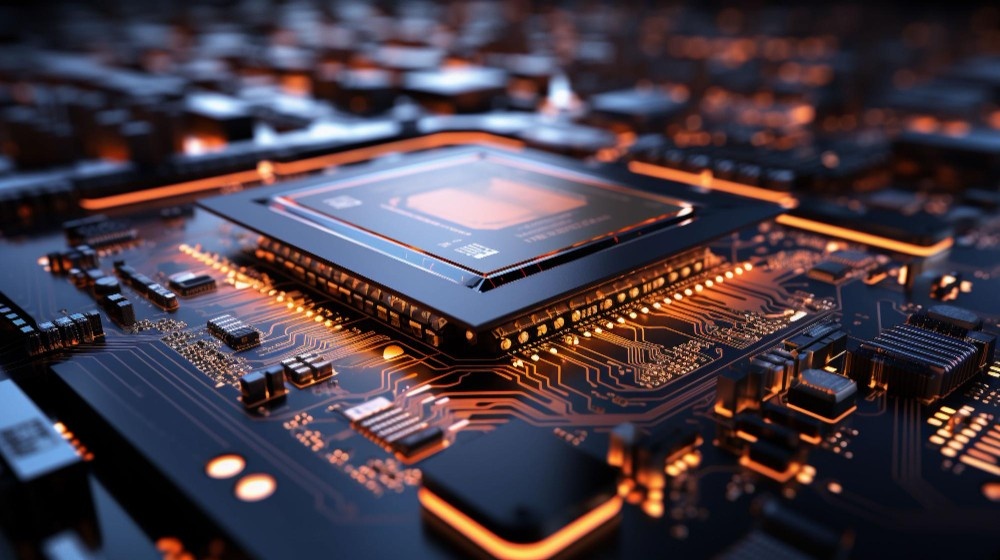
The Role of MEP Systems in Semiconductor Manufacturing
Almost all the modern devices rely on semiconductors, including smartphones, computers, advanced medical devices, and autonomous vehicles.
To ensure that these delicate components are produced with precision and efficiency, semiconductor manufacturing requires highly specialized systems. Among the most critical of these are Mechanical, Electrical, and Plumbing (MEP) systems.
A reliable MEP system is essential to maintaining the controlled environment required for semiconductor production, ensuring operational efficiency and product quality. VMS Consultants are renowned as the best structural consultant in Ahmedabad, providing expert solutions for complex engineering challenges.
This article explores why MEP systems are crucial to semiconductor manufacturing.
Understanding the Importance of MEP Systems in Semiconductor Manufacturing
Semiconductor manufacturing is a highly intricate process that demands precision and control. A cleanroom environment is essential for these processes, where tiny particles, temperature, humidity, and airflow must be meticulously regulated.
This is where MEP systems come in.
These systems manage everything from the HVAC (Heating, Ventilation, and Air Conditioning) systems to water and gas distribution, making them indispensable in maintaining the required conditions for manufacturing.
The Role of MEP Systems in Semiconductor Manufacturing
1. HVAC Systems for Temperature and Humidity Control
In semiconductor fabrication, maintaining the correct temperature and humidity is critical. Even the smallest deviation can result in defects in the final product.
HVAC systems are responsible for regulating the temperature, ensuring that cleanroom conditions are met. These systems maintain air purity and prevent the introduction of particles that could contaminate the sensitive semiconductor components.
Moreover, these systems help control humidity levels, which is crucial for the prevention of electrostatic discharge (ESD). ESD can cause irreparable damage to semiconductors, making it essential to maintain a stable and controlled environment.
2. Air Filtration and Cleanroom Standards
Semiconductor fabrication facilities rely heavily on air filtration systems to remove contaminants such as dust, chemicals, and other particulates from the air. These systems ensure that the air in the cleanroom is free from pollutants, as even microscopic particles can impact the manufacturing process.
Robust filtration systems, including High-Efficiency Particulate Air (HEPA) and Ultra-Low Particulate Air (ULPA) filters, are essential to maintaining the stringent air quality standards required for semiconductor production.
3. Water Supply and Distribution
Water is another critical element in semiconductor manufacturing. It is used in various stages of the process, such as cleaning the wafers and cooling the equipment.
However, the water used in these processes must be of the highest purity, often requiring the use of deionized or ultrapure water (UPW).
A reliable MEP system ensures that water is supplied in the required quantity and quality, with systems in place for treatment, storage, and distribution. The careful management of water ensures that contamination risks are minimized, and production processes are not disrupted due to water supply issues.
4. Gas Supply and Distribution Systems
Semiconductor manufacturing requires various gases for processes such as etching and deposition. Gases like nitrogen, oxygen, hydrogen, and various specialty gases are integral to these procedures.
An MEP system ensures that these gases are supplied in the correct quantities and pressures, without any leakage or contamination.
The distribution systems for these gases must be designed with precision, as any fluctuation in gas flow or pressure can negatively impact the quality of the semiconductor products.
MEP systems are also responsible for ensuring the safety of these systems, as the gases used in semiconductor manufacturing can be hazardous.
Key Components of MEP Systems in Semiconductor Facilities
1. Mechanical Systems
Mechanical systems within semiconductor facilities include HVAC systems, air handling units, cooling systems, and other essential equipment designed to regulate the internal environment. These systems must be capable of providing 24/7 operation with minimal downtime, as even brief disruptions can cause costly delays in production.
2. Electrical Systems
Electrical systems in semiconductor manufacturing facilities control the power supply to critical equipment and machinery. They also ensure the availability of backup power sources in case of outages.
Uninterruptible Power Supply (UPS) systems and backup generators are integral to maintaining continuous operations. Any disruption to electrical power can halt production and lead to significant losses.
3. Plumbing Systems
Plumbing systems in semiconductor facilities are designed to manage the supply and drainage of ultrapure water and other liquids required in the production process. These systems are critical to maintaining the necessary standards for water quality and ensuring that wastewater is safely disposed of or recycled.
4. Safety and Monitoring Systems
Given the complex and sensitive nature of semiconductor manufacturing, safety is a top priority. MEP systems incorporate safety measures such as gas detection systems, fire suppression systems, and emergency shut-off valves to ensure a safe working environment.
Continuous monitoring of air quality, water purity, temperature, and humidity is essential for detecting any deviations from the ideal conditions before they affect the production process.
Major Challenges in Designing and Implementing MEP Systems for Semiconductor Manufacturing
Designing MEP systems for semiconductor manufacturing involves several challenges due to the complexity and precision required.
Some of these challenges include:
1. High Energy Consumption
Semiconductor manufacturing is energy-intensive, and MEP systems must be designed to optimize energy efficiency while maintaining the necessary operating conditions. HVAC systems, in particular, can account for a significant portion of energy usage in semiconductor facilities, making energy-efficient design a crucial consideration.
2. Space Constraints
Semiconductor manufacturing facilities often have limited space, particularly in cleanrooms where space utilization is tightly controlled. MEP systems need to be compact and efficient, ensuring that they provide the necessary services without occupying valuable space that could be used for production.
3. Stringent Regulatory Requirements
Semiconductor manufacturing is subject to strict regulatory standards regarding environmental control, safety, and waste management. MEP systems must meet these regulatory requirements, ensuring that the facility operates in compliance with national and international standards.
4. Integration with Other Systems
MEP systems in semiconductor facilities must be seamlessly integrated with other systems, such as the manufacturing equipment and production lines. Any disruption or failure in one system can affect the entire operation, so integration must be carefully planned and executed.
The Role of VMS Consultants in MEP System Design and Implementation
VMS Consultants, Best Structural Consultant in Ahmedabad, specializes in providing engineering, architecture, and project management services for industries such as semiconductor manufacturing.
We work closely with our clients to design and implement MEP systems that are efficient, safe, and comply with environmental control.
We ensure that your semiconductor manufacturing facility operates smoothly with minimal downtime, while also meeting all regulatory requirements and sustainability goals. Our experience in MEP system design and implementation makes us a trusted partner in optimizing your facility’s operations.
For more information on how VMS Consultants can help you with the design and implementation of MEP systems, get in touch with us today!