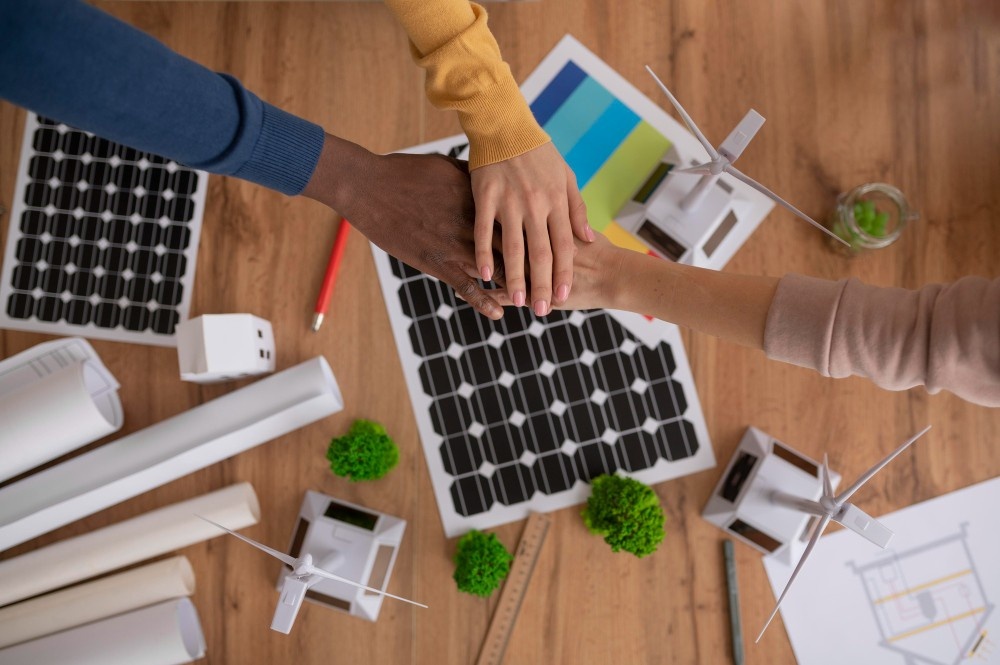
A Guide to Supply Chain of Solar Panel Manufacturing Parts
As solar energy gains momentum in India, the need for efficient and high-quality solar panel manufacturing has become more critical than ever. Solar panels require a complex assembly of parts sourced from different suppliers, making the supply chain an important factor.
A well-optimized supply chain not only enhances the efficiency of manufacturing processes but also contributes to the overall quality and affordability of solar panels.
In this article, we will explore the supply chain involved in solar panel manufacturing, covering the key parts required, challenges faced, and how factories can optimize the supply chain for timely & cost-effective production.
Raw Materials
Solar panels are made from raw materials like silicon, copper, aluminum, and glass.
Silicon is the primary material for solar cells, while copper is commonly used in wiring and connections. Aluminum is essential for frames, and glass provides a protective covering.
India has an advantage in sourcing some of these materials locally, but others, like high-purity silicon wafers, are often imported.
Efficiently managing the sourcing of these materials is the first step in building a strong supply chain, ensuring materials are readily available to avoid production delays.
Solar Cells
The solar cell is the most important part of a solar panel, responsible for converting sunlight into electricity. These cells are made from processed silicon, which is highly purified and crystallized to achieve optimal energy conversion.
Manufacturers often rely on a variety of suppliers for solar cells, particularly because of the demand for different types, such as monocrystalline and polycrystalline cells. The choice of suppliers depends on factors like cell quality, lead time, and cost.
In India, securing reliable suppliers for solar cells can be challenging due to high demand, but long-term partnerships with reputable vendors can ensure consistent supply and pricing.
Glass and Encapsulant Materials
A solar panel’s glass layer is responsible for protecting the solar cells from weather, dust, and physical impacts. High-quality, low-iron glass is often used to allow maximum sunlight to penetrate while ensuring durability.
Encapsulants, typically ethylene-vinyl acetate (EVA), hold the cells in place and protect them from moisture. Both materials are typically sourced from specialty suppliers, and ensuring their quality is critical for extending the panel’s life.
In the Indian market, identifying suppliers with experience in high-quality glass and encapsulants is key to maintaining durability standards.
Back Sheets and Frames
The back sheet of a solar panel serves as a protective layer, guarding against moisture and UV radiation.
Frames, usually made of aluminum, provide structure and stability. Both components must be sourced with care to ensure they meet environmental durability standards.
Local sourcing for these materials can reduce costs and support the “Make in India” initiative. However, it’s essential to partner with suppliers who adhere to international quality standards to produce panels that are both cost-effective and reliable.
Wiring and Connectors
Though small, wiring and connectors are necessary for efficient power transmission in solar panels. High-quality copper wiring and reliable connectors ensure the smooth flow of electricity with minimal loss.
Poor-quality wiring can lead to energy loss and safety hazards, so it’s essential to source these parts from suppliers known for durability. For Indian manufacturers, sourcing connectors locally or from nearby regions can help control costs and maintain supply reliability.
Inverters and Junction Boxes
Inverters convert the direct current (DC) generated by solar panels into alternating current (AC) that can be used in homes and businesses. Junction boxes house the electrical connections within the panel and are equipped with bypass diodes to prevent hot spots.
While not physically part of the panel, inverters and junction boxes are critical to system functionality. Indian manufacturers often partner with specialized suppliers for these components to ensure they meet electrical and safety standards.
Supply Chain Challenges
The solar panel manufacturing supply chain is complex, with multiple components sourced from different suppliers. This complexity can lead to several challenges, including:
Supply Delays: Any delay in a single part can halt production, impacting project timelines and costs.
Cost Variations: Price fluctuations in raw materials, particularly silicon and copper, can affect overall manufacturing costs.
Quality Control: Ensuring consistent quality across all suppliers is crucial to prevent defects and maintain product reliability.
For Indian factories, overcoming these challenges requires strategic planning, vendor management, and quality assurance practices to ensure both cost-effectiveness and high-quality output.
How to Overcome These Supply Challenges?
Optimizing Inventory Management
Effective inventory management is essential for maintaining a steady supply of parts without overstocking. Just-in-Time (JIT) inventory, where parts are ordered based on immediate production needs, is commonly used in solar panel manufacturing to reduce holding costs.
Indian factories, which often face space and budget constraints, can benefit from JIT.
However, this strategy requires close coordination with suppliers to prevent delays. Building a reliable forecasting system based on production demands and market trends can also help factories maintain optimal stock levels.
Vendor Relationships
Strong vendor relationships are a key part of an optimized supply chain. By building long-term partnerships with trusted suppliers, manufacturers can ensure consistent quality and timely delivery, even during high-demand periods.
In India, where demand for solar parts is growing rapidly, establishing partnerships with reliable suppliers can provide a competitive advantage. Such relationships may also lead to negotiated prices and priority in supply, helping factories to maintain cost efficiency and timely production.
Leveraging Technology
Supply chain technology can significantly enhance visibility, allowing manufacturers to monitor shipments, manage inventory, and anticipate disruptions. Systems like Enterprise Resource Planning (ERP) or Supply Chain Management (SCM) software can provide real-time data on part availability, delivery schedules, and supplier performance.
For Indian manufacturers, investing in supply chain technology can make the difference between meeting project deadlines and facing costly delays. It also improves transparency, making it easier to identify bottlenecks and optimize the overall workflow.
Localizing the Supply Chain
Given India’s push for local manufacturing, sourcing parts from domestic suppliers can help reduce dependency on imports, which are often subject to delays, tariffs, and exchange rate fluctuations. Developing a local supply chain also aligns with government incentives, supporting the “Make in India” initiative while reducing lead times.
However, while local sourcing offers advantages, it’s essential for manufacturers to ensure that domestic suppliers meet quality standards. Balancing the benefits of local suppliers with international quality requirements is key to creating a sustainable supply chain.
Conclusion
For Indian solar component manufacturers, overcoming supply chain challenges through effective inventory management, local sourcing, and strategic partnerships can help meet the growing demand for solar energy while maintaining competitive pricing.
An optimized supply chain can make all the difference in an industry where quality control and timely production are a must.
For expert guidance on managing supply chains for solar panel manufacturing, reach out to VMS Consultants today. With our extensive experience in renewable energy factory consultancy, we can help you build a streamlined, efficient production process together!