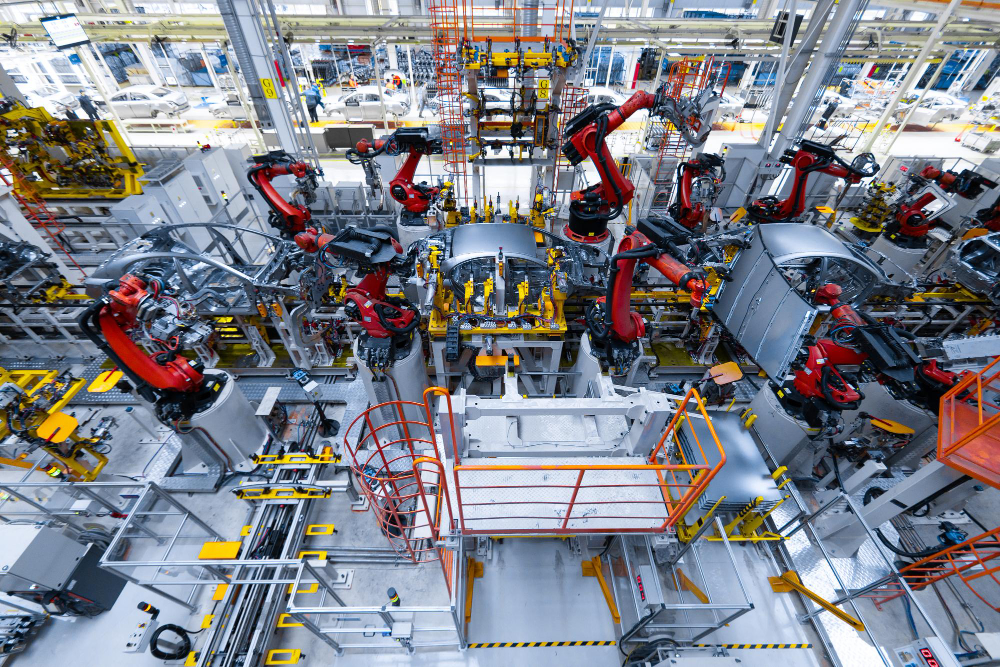
How You Can Optimize Factory Layout for Shortened Production Lead Times?
A well-planned factory layout enhances efficiency and reduces production lead times in an industrial environment. Organization improves productivity and profitability by reducing wasted time and resources, improving workflow and reducing waste.
Taking a strategic approach to factory layout in India can significantly reduce production lead times, enabling quicker delivery to the market, where operational efficiency is key.
In this article, we explore how to optimize factory layout and offer actionable insights on how to do so.
What is Production Lead Times?
Production lead time is the total time taken from the initiation of a production process to its completion.
It includes every stage, from the procurement of raw materials to the dispatch of the final product. By reducing lead times, factories are able to respond more quickly to market demands, reduce inventory costs, and increase productivity.
Long lead times are often caused by inefficient factory layouts, which result in poor organization, bottlenecks, and unnecessary movement of materials and workers.
5 Key Considerations for Optimizing Factory Layout
Below are some key considerations that can help in achieving an optimized layout:
1. Streamlining Material Flow
Material flow is one of the most critical aspects of an optimized factory layout. Ideally, the layout should minimize the distance that materials must travel between stages of production. Workstations should be arranged in a sequential order that mirrors the production process.
For example, placing the assembly line close to the warehouse where raw materials are stored can reduce the time and effort required to transport materials, leading to shorter lead times.
2. Reducing Bottlenecks
Bottlenecks occur when one stage of the production process is slower than the others, causing delays and increasing lead times. Identifying and addressing these bottlenecks is essential for optimizing factory layout.
The process can involve reconfiguring workstations, adding additional equipment, or redistributing workloads to ensure that all stages of production run smoothly.
3. Enhancing Workstation Ergonomics
Worker productivity is directly influenced by the ergonomics of their workstations. An optimized layout should prioritize the comfort and safety of workers by ensuring that tools and materials are easily accessible, reducing the need for unnecessary movement and strain.
Ergonomically designed workstations not only improve worker efficiency but also reduce the risk of workplace injuries, leading to fewer disruptions and shorter lead times.
4. Implementing Lean Manufacturing Principles
Lean manufacturing principles focus on eliminating waste and optimizing processes to improve efficiency. These principles can be applied to factory layout design by identifying and removing non-value-added activities, such as excessive transportation, waiting times, and overproduction.
For example, adopting a cellular manufacturing approach, where workstations are grouped by product families, can reduce movement and improve coordination between different stages of production.
5. Flexibility for Future Expansion
An optimized factory layout should not only address current production needs but also allow for future expansion and changes in product lines. As markets change rapidly, factories must be flexible to adapt quickly to new demands.
Conclusion
The layout of a factory plays a significant role in reducing production lead times and improving overall efficiency.
With the help of VMS Consultants, you can design and implement an optimized factory layout that meets your production objectives. As the leading factory project consultant in India, we have helped hundreds of clients reach their goals.
Contact us today to enhance your factory’s efficiency and reduce lead times!