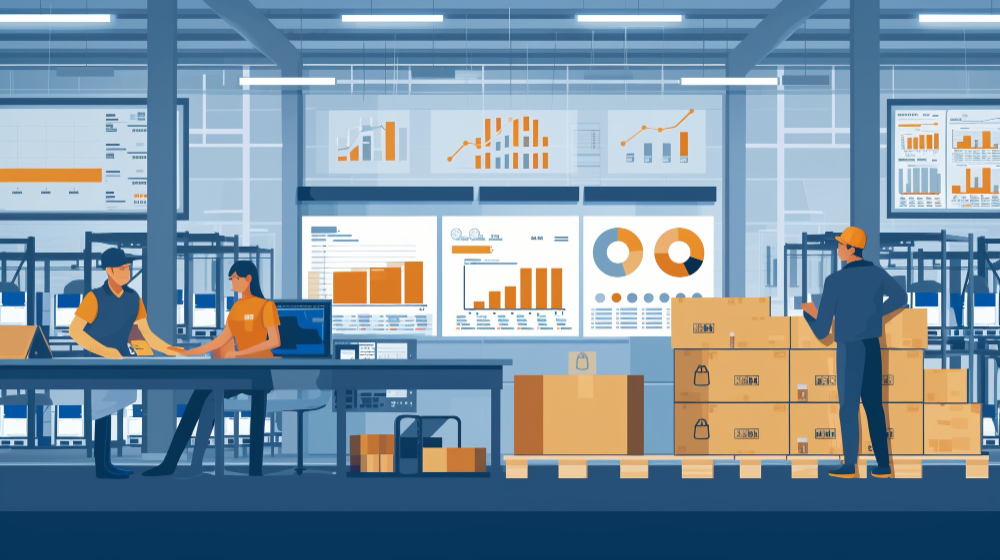
How to Implement a Kanban System for Just-in-Time Production?
Just-in-time (JIT) production is a strategy that focuses on producing only what is needed when it is needed, minimizing waste and reducing inventory costs.
One effective way to implement JIT production is through a Kanban system.
In this article, we examine how to implement a Kanban system for JIT production, highlighting its benefits and practical steps for implementing it successfully.
What is Kanban?
Kanban, which translates to “visual signal” in Japanese, is a scheduling system that helps manage workflow and inventory in a way that aligns production with demand.
Originating from Toyota’s manufacturing processes, Kanban uses visual cues, such as cards or boards, to signal when to produce more items or move them through different stages of the production process.
This method emphasizes transparency, flexibility, and continuous improvement, making it ideal for JIT production.
Benefits of a Kanban System
Implementing a Kanban system offers numerous benefits for businesses seeking to enhance their JIT production processes:
Reduced Lead Times: By signaling when to produce more items, Kanban helps reduce lead times and ensures that products are available when needed.
Improved Workflow: The visual nature of Kanban helps teams identify bottlenecks and inefficiencies in the production process, leading to smoother operations.
Enhanced Flexibility: Kanban allows for quick adjustments to production schedules based on changes in demand, making it easier to respond to customer needs.
Minimized Inventory Costs: JIT production minimizes excess inventory, leading to lower holding costs and reduced risk of obsolescence.
Increased Employee Engagement: Kanban empowers employees by giving them visibility and control over their tasks, fostering a culture of collaboration and continuous improvement.
Steps to Implement a Kanban System for JIT Production
Implementing a Kanban system requires careful planning and execution. Here are key steps to ensure successful implementation:
1. Assess Current Processes
Before implementing Kanban, evaluate your current production processes. Identify areas where you experience delays, excess inventory, or inefficiencies. Gather input from employees at all levels, as their insights will help pinpoint specific pain points.
2. Define Your Workflow
Clearly define the workflow for your production process. Map out each step, from receiving raw materials to shipping finished products. This visualization will serve as the foundation for your Kanban system, ensuring everyone understands the flow of work.
3. Determine Inventory Levels
Establish the appropriate inventory levels for each stage of production. This includes determining how many items should be in process and how many should be available as finished goods. A Kanban system relies on setting these thresholds to maintain JIT production.
4. Create Kanban Signals
Develop the visual signals that will indicate when to start production or reorder materials. These signals can take various forms, such as physical cards, colored bins, or digital alerts. The key is to ensure that the signals are easily recognizable and accessible to all team members.
5. Implement the Kanban Board
A Kanban board is a powerful tool for managing the workflow. It typically consists of columns representing different stages of production (e.g., To Do, In Progress, Done) and cards representing individual tasks or items. Place the Kanban board in a visible location where the entire team can monitor progress and make updates in real time.
6. Train Employees
Training is crucial for the successful implementation of a Kanban system. Educate employees on how to use the Kanban signals and the board effectively. Emphasize the importance of communication and collaboration, as successful JIT production relies on teamwork.
7. Monitor and Adjust
Once the Kanban system is in place, continuously monitor its effectiveness. Collect data on production times, lead times, and inventory levels. Encourage team members to provide feedback on the system, and be prepared to make adjustments as needed to optimize the process.
Conclusion
Implementing a Kanban system for just-in-time production can significantly enhance your manufacturing processes.
As you explore the benefits of a Kanban system, consider partnering with VMS Consultants, leading industrial PMC in India. We specialize in engineering, architecture, and project management services tailored to various industrial segments.
Be sure to check back for more such information!