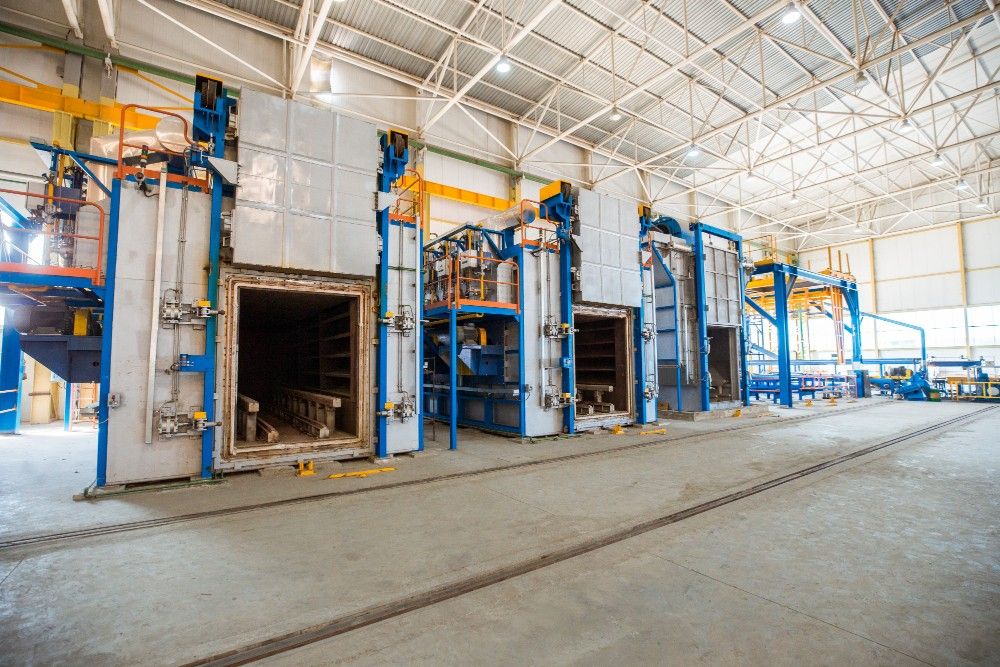
Steps for Equipment Installation in a Factory Building
Installing equipment in a factory building is a crucial process that requires meticulous planning, coordination, and execution to ensure efficiency, safety, and compliance with regulations. Whether it’s setting up heavy machinery or integrating complex systems, each step in the installation process plays a vital role in the overall functionality and productivity of the facility. In this article, we will explore the comprehensive steps involved in equipment installation in a factory building, highlighting key considerations and best practices.
Step 1: Pre-Installation Preparation
Before any equipment is installed, thorough planning and preparation are essential. This stage involves several key activities:
- Site Survey and Assessment:
– Conduct a detailed survey of the factory building to assess available space, access points, utility connections (such as electricity, water, and gas), structural integrity, and any potential obstacles or hazards.
– Identify specific locations where equipment will be installed, considering factors like workflow efficiency and safety regulations.
- Equipment Selection and Procurement:
– Choose equipment that meets operational requirements, considering factors such as capacity, efficiency, maintenance needs, and compatibility with existing systems.
– Coordinate with suppliers and manufacturers to ensure timely delivery and readiness of equipment for installation.
- Safety and Regulatory Compliance:
– Review safety protocols and regulatory requirements applicable to the installation of specific types of equipment (e.g., electrical safety standards, environmental regulations).
– Obtain necessary permits and approvals from regulatory authorities before commencing installation activities.
- Logistics and Scheduling:
– Develop a detailed installation schedule that accounts for sequential installation of equipment, dependencies between tasks, and allocation of resources (such as manpower and equipment handling tools).
– Coordinate logistics for transporting equipment to the site, ensuring proper handling and storage to prevent damage.
Step 2: Installation Process
Once the preparatory phase is complete, the actual installation process begins. This phase includes the following steps:
- Foundation and Structural Preparation:
– If required, prepare foundations or structural supports for heavy machinery, ensuring they meet load-bearing specifications and are aligned with manufacturer recommendations.
– Conduct structural reinforcement if necessary to accommodate the weight and operational dynamics of the equipment.
- Mechanical Assembly:
– Assemble mechanical components of the equipment according to manufacturer guidelines and technical drawings.
– Ensure proper alignment and calibration of moving parts, fasteners, and assemblies to optimize operational efficiency and longevity.
- Electrical and Instrumentation Installation:
– Install electrical wiring, control panels, sensors, and instrumentation systems according to electrical diagrams and specifications provided by the equipment manufacturer.
– Test electrical connections for continuity, insulation resistance, and compliance with safety standards to prevent electrical hazards.
- Fluid Connections and Plumbing:
– Connect fluid lines (such as water, air, or hydraulic lines) to the equipment, ensuring proper sealing, pressure testing, and compliance with fluid handling standards.
– Install plumbing fixtures and drainage systems as required to support equipment operation and maintenance.
- Integration and System Testing:
– Integrate the installed equipment with existing factory systems (e.g., production lines, automation systems) to ensure seamless operation and data exchange.
– Conduct comprehensive system tests to verify functionality, performance, and safety compliance before final commissioning.
Step 3: Commissioning and Handover
After completing the installation process, the equipment undergoes commissioning to prepare it for operational use. This phase involves:
- Functional Testing and Adjustment:
– Perform operational tests to validate equipment performance under normal operating conditions.
– Make necessary adjustments to optimize settings, alignments, and controls based on test results and operational requirements.
- Training and Documentation:
– Provide training sessions for operational staff on equipment usage, maintenance procedures, and safety protocols.
– Prepare comprehensive documentation including operation manuals, maintenance schedules, and troubleshooting guides for future reference.
- Final Inspection and Certification:
– Conduct a final inspection to ensure all installation and commissioning activities comply with regulatory standards and contractual requirements.
– Obtain certification or approval from relevant authorities confirming the equipment’s readiness for operational deployment.
- Handover to Operations:
– Formalize the handover process by transferring ownership and operational responsibility of the equipment to the factory’s operations team.
– Address any outstanding issues or concerns identified during commissioning to ensure smooth transition to regular production activities.
Step 4: Post-Installation Support and Maintenance
Even after successful installation and commissioning, ongoing support and maintenance are crucial to sustain equipment performance and longevity:
- Routine Maintenance:
– Implement a preventive maintenance program to inspect, clean, and lubricate equipment components regularly.
– Schedule periodic maintenance shutdowns to address wear and tear, replace consumable parts, and recalibrate systems as needed.
- Monitoring and Performance Optimization:
– Monitor equipment performance through data analytics, sensors, and feedback from operators to identify opportunities for efficiency improvements.
– Implement continuous improvement initiatives to optimize energy consumption, production output, and overall operational efficiency.
- Emergency Response and Repairs:
– Establish protocols for responding to equipment failures or emergencies, including rapid troubleshooting, spare parts inventory management, and emergency repair services.
– Maintain a network of qualified service providers and technicians capable of addressing complex technical issues promptly.
Wrapping Up
The installation of equipment in a factory building involves a systematic approach encompassing planning, execution, and post-installation support. Each step in the process—from pre-installation preparation to commissioning and ongoing maintenance—plays a critical role in ensuring the reliability, safety, and efficiency of factory operations. By adhering to best practices and regulatory requirements, manufacturers can minimize risks, maximize productivity, and enhance the overall operational performance of their facilities. Effective equipment installation not only lays the foundation for operational success but also contributes to long-term sustainability and competitiveness in the manufacturing industry.