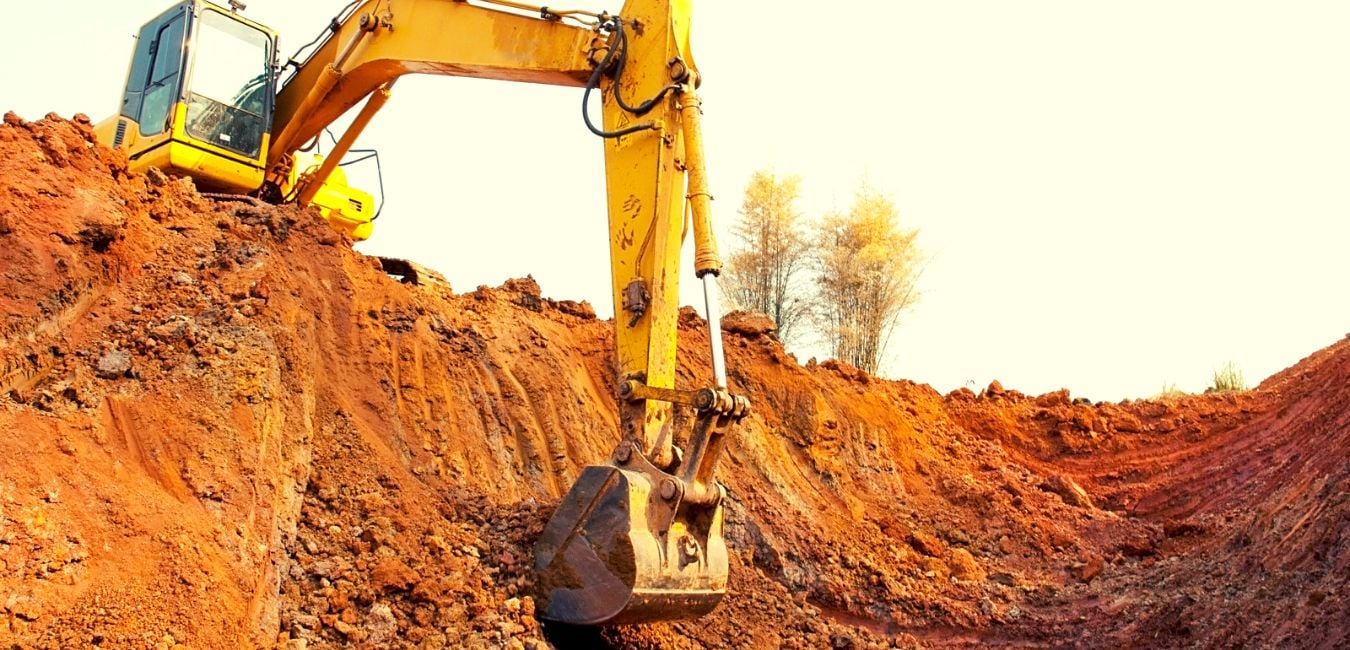
Do you need to undertake filling on your industrial project’s land? What are the costs involved?
General Introduction
The process of land filling is a regular practice in the industrial construction project sector. Land filling, in construction, is carried out for levelling the land and to create a suitable surface for the construction of industrial facilities. However, the land filling process is not always required for industrial construction projects, and the decision to fill or not to fill land depends on several factors. In this article, we will be discussing the reasons why filling may be necessary, how to analyse if filling is required for your industrial project, and the costs involved in filling land for industrial building projects.
Why is Filling Essential for Industrial Construction Projects?
Filling land is often a requirement for industrial construction for several reasons, which includes:
To level the land – Filling is essential to level a surface evenly for the construction of industrial facility. Levelling is particularly needed when the land is located in a hilly or sloping area.
To increase the elevation – In some cases, land filling becomes necessary to increase the elevation of the land, especially if the area is prone to flooding.
To improve soil quality – Land filling can enhance the quality of soil and also increases its load-bearing capacity, which is essential for heavy industrial machinery and equipment.
To meet building code requirements – In some regions, land filling is carried out to meet building code requirements for industrial construction projects.
How to Analyse if Filling is Required for Your Industrial Project?
Several factors need to be considered when analysing if filling is required for your industrial project. These factors include:
Topography of the industrial construction site – The topography of the site plays a significant role in determining if filling is necessary. If the site is sloping or hilly, filling may be required to create a levelled surface.
Quality of soil – The quality of the soil is another factor that needs to be considered. If the soil is not suitable for construction, filling may be necessary to enhance soil quality and increase its load-bearing capacity.
Environmental Factors – Environmental factors such as flood zones, erosion, and soil instability can also play a role in determining if land filling is necessary.
Building Code Requirements – Building code requirements in your area may mandate filling land for industrial projects.
Cost Analysis – Filling land can be expensive, so it’s important to conduct a cost survey to determine if filling is a cost-effective option.
Costs Involved in Filling Land for Industrial Projects
The cost of land filling for a typical industrial construction project depends on several factors, including the size or the area of the project, the type of material used, and the extent of work required. Some of the potential costs involved in filling land for industrial projects include:
Excavation and Grading – Excavation and grading can turn out to be expensive, especially if the project site is large or difficult to access.
Soil or Filler Material Costs – The cost of the soil or other filler materials used for land filling can vary depending on the type and quality of material required.
Transportation and Delivery Costs – Depending on the location of the project site and the source of the filler material, the transportation cost can increase significantly.
Labor Costs – The cost of labor for the land filling work can be a significant expense if the work is complex or requires specialised expertise.
Permits and Regulatory Costs – Depending on the location of the site and the local regulations, you may need to acquire permits for your industrial project or pay fees for the filling work.
Wrapping Up
To conclude, determining whether land filling is required on an industrial project’s land depends on several factors, such as the existing topography, soil quality, and the intended use of the site. A thorough site analysis and consultation with a professional contractor or engineering firm can assist in evaluating whether land filling would be necessary and what type of filler material is required for the same. The costs involved in land filling can extensively vary, depending on factors such as excavation and grading, soil or material costs, transportation and delivery costs, labor costs, and permit fees. It is, however, important to plan out carefully for these costs to avoid cost overruns and delays in project completion. By carefully considering the site conditions and budget planning appropriately, industrial projects can be successfully completed with a levelled, stable foundation that supports safe and efficient operations.